Для чего применяется метод зенкерования отверстий?
При монтаже некоторых металлоконструкций и узлов оборудования используются винты с потайной или полупотайной головками. Обычные отверстия для этой цели непригодны. Для того, чтобы получить на одном из торцов отверстия коническую фаску, необходимо применить такую операцию, как зенкерование (или, иначе - зенковку). Её можно выполнить на обычном сверлильном станке, установив специальный инструмент – зенкер.
Назначение и виды зенкеров
В результате зенковки образует коническое отверстие, совпадающее с углом наклона винта. Когда винт полностью затянут, головка будет располагаться заподлицо или немного ниже поверхности прижима крепежа к детали.
Зенкера имеют большой диапазон применений и углов. Стандартные размеры включают угла наклона рабочей части от 60 до 90°. Менее распространены инструменты, имеющие угол конической части 100°, 110° и 120°. Наличие угла позволяет успешно использовать зенкеры для удаления заусенцев или снятия фасок на углах изделий.
Известны различные исполнения зенковок, и у каждой из них есть свои отличительные особенности и преимущества.
Важно: технические требования к рассматриваемой оснастке отечественного производства регламентируются нормами ГОСТ 12489-71(цельные зенкера) и ГОСТ 21582-76 (торцовые зенкера).
Сам инструмент состоит из:
-
рабочей части в виде конуса;
-
переходной части, форма обеспечивает минимизацию внутренних напряжений и отвод стружки, образующейся в процессе резания;
-
посадочной части или хвостовика, которым зенкер присоединяется к шпинделю станка.
Рабочая часть зенковки может быть цельной или составной. Последний вариант реализуется в твердосплавной оснастке и применяется при зенкеровании отверстий в труднообрабатываемых деталях из высокоуглеродистых сталей, а также в условиях массового производства. Сменные вставки могут изготавливаться и из быстрорежущих сталей. Соединение вставки с корпусом производится при помощи пайки медью, для изготовления корпуса вставки могут быть использованы конструкционные среднелегированные стали типа 30ХГСА, 40 ХНМ и пр., а сами вставки производят из твёрдых сплавов ВК15 или ВК20.
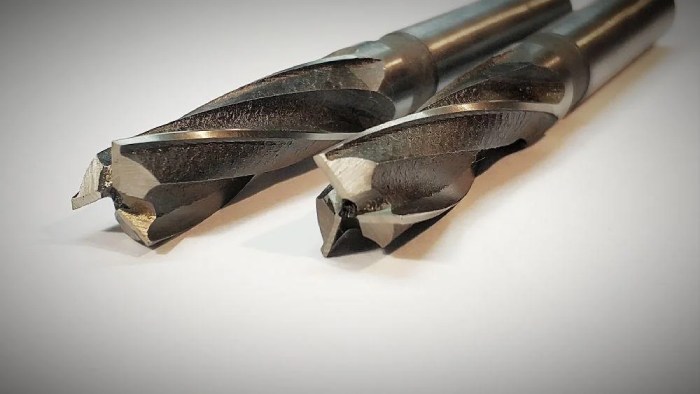
Зенкера, которые изготовлены без стружкоотводящих канавок, имеют форму конуса с желаемым внутренним углом. Они используются в единичном производстве, могут быть сплошными и полыми. В последнем случае улучшаются условия охлаждения инструмента. Часто конструкция оснастки предусматривает наличие и бокового отверстия. Оно просверливается через периферическую часть конуса и имеет зазор для обеспечения свободного резания. При длительной протекающих процессах механической обработки через полую часть зенкера может подаваться смазочно-охлаждающая жидкость.
Зенкерование отверстий иногда предусматривает обработку обратной стороны просверлённого или резьбового отверстия. Хвостовик такого инструмента вставляется в готовое отверстие, а на тыльной стороне монтируется фреза. Затем инструмент поворачивают и выполняют операцию снятия фаски или торцевания.
Значительно реже конструируют зенкера-фрезы, в которых предусматриваются поперечные отверстия, имеющие угол наклона около 45° к оси зенкования. Это отверстие в головке образует две режущие кромки. Через боковое отверстие отводится стружка, что предотвращает её застревание между инструментом и заготовкой. Это очень важно при значительном объёме удаляемого металла, поскольку заклинивание стружки приводит к поломке оснастки.
Существуют комбинированные варианты данной оснастки: сверло + зенкер. Они используются для изготовления центра на конце круглого изделия, чтобы лучше удерживать деталь при её обработке на токарном станке или станке с ЧПУ.
Чем зенкерование отличается от смежных операций
Важно: основное отличие заключается в размерах зоны обработки. При зенкеровании она локализуется в торцевой части обрабатываемого изделия, в то время, как, например, при сверлении плавно перемещается по глубине получаемого отверстии. Из-за этого условия теплоотвода улучшаются, поэтому зенковки перегреваются гораздо реже свёрл.
Процесс зенкования начинается с врезки инструмента в торцевую часть просверлённого отверстия. Последовательность врезания зависит от конструкции зенкера:
-
с плоской рабочей частью;
-
с фасонной рабочей частью;
-
с конической рабочей частью.
Зенкера первого типа наиболее универсальны, их можно, в частности, использовать для операций шлифовки или формообразования торца. Твёрдость такой оснастки выше обычной и составляет 60…63 HRC. Зенковки с плоским торцем используются для изготовления торцевых полостей под винты с цилиндрической головкой и под болты с шестигранной головкой.
Фасонные зенковки можно применять не только для получения фасок, но и для шлифования, но не плоского, а объёмного. Для таких зенкеров необходимо наличие центрального охлаждающего отверстия.
Конические зенковки больших размеров также снабжаются охлаждающими отверстиями и этим отличаются от стандартного шлифовального или сверлильного инструмента.
Важным технологическим параметром данной оснастки считается угол конической части, который составляет:
-
60° - при снятии заусенцев;
-
75° - для головок потайных заклепок;
-
90° - для винтов с потайной головкой;
-
120° - при зенковке листового металла.
Количество режущих кромок - обычно нечётное, что гарантирует плавность перемещения рабочего инструмента во время обработки хода. Стружка удаляется через профиль канавки.
Хвостовики зенкеров изготавливают в четырёх различных версиях: цилиндрический хвостовик, конус Морзе, хвостовик насадки и трёхсторонний хвостовик. В последнем случае предотвращается проскальзывание инструмента в патроне сверлильного станка. Такие зенкеры можно устанавливать даже в ручную дрель, выполняя сверление-зенкерование за один проход.
Технология зенкерования
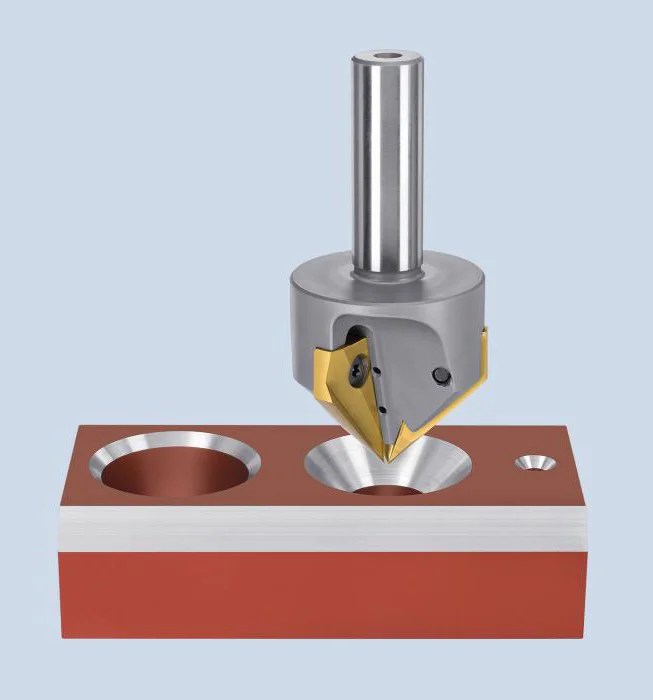
Зенкерование обычно является завершающей операцией подготовки отверстий, предназначенных для соединения деталей. Зенковка отверстия расширяет зону входа и облегчает, например, установку резьбового сверла.
Подготовка торца отверстия под последующее зенкерование включает очистку его внутренней части от остатков стружки (полезно ещё раз пройтись сверлом в готовом отверстии). Далее, с той же установки станка производится замена оснастки и выполняется подготовка фаски.
Обычно на конце кромки просверлённого отверстия образуются небольшие частицы материала, которые спиральным сверлом выдавливаются в сквозное отверстие. Такие частицы называются заусенцами. Заусенцы обладают очень острыми краями и представляют риск травмирования рабочего. Поэтому после сверления следует удалить заусенцы, не только из соображений безопасности, но и для улучшения внешнего вида просверленного отверстия.
Зенкерование может быть с успехом использовано для удаления краевых заусенцев. Чаще используется инструментальная оснастка с углом зенковки 60 °, хотя можно использовать зенкеры и с другими углами наклона конической части.
Важно: в зенковках комбинированного типа операции сверления и зенкерования могут быть совмещены, что снижает трудоёмкость обработки изделий. Подачу за один оборот шпинделя для металла повышенной твёрдости следует несколько снижать.
Все тесты
- Английский язык
- Биология
- История
- Физкультура
- Пушкин А.С
- Религия
- Карьера
- Информатика
- Физика
- Стихи
- Обществознание
- Сочинения
- ОБЖ
- Экономика
- Окружающий мир
- Помощь студенту
- География
- Подготовка к ЕГЭ
- Математика
- Пунктуация
- Правоведение
- Орфография
- Анализ стихотворений
- Краткие содержания
- Биографии
- Литература
- Русский язык
- Фонетический разбор
- Тест на тему История сибирской язвы и как она стала оружием 5 вопросов
- Тест на тему Что такое “железное легкое” и как жилось узникам аппарата 5 вопросов
- Тест на тему Суть и методы клеточной инженерии 5 вопросов
- Тест на тему Злаковые растения - общая характеристика, признаки и список представителей 7 вопросов
- Тест на тему Семейство бобовые - общая характеристика, строение и представители 7 вопросов
- Тест на тему Красный и белый террор в годы Гражданской войны 5 вопросов
- Тест на тему История появления имущественного неравенства и знати 5 вопросов
- Тест на тему Народы, населявшие Россию во второй половине 16 века 5 вопросов
- Тест на тему Первые государства: история образования и функции 5 вопросов
- Тест на тему Роль огня в жизни первобытных и современных людей 5 вопросов
- Тест на тему 5 самых известных разведчиков в истории 5 вопросов
- Тест на тему Присоединение к Московскому государству Смоленска 5 вопросов
- Тест на тему Причины и предпосылки объединения русских земель вокруг Москвы 5 вопросов
- Тест на тему Формирование русского централизованного государства 5 вопросов
- Тест на тему Краткая история Руси в 15 веке: главные события, культура 5 вопросов
- Тест на тему Причины и итоги установления автокефалии Русской Церкви 5 вопросов
- Тест на тему Особенности общественного строя и церковной организации на Руси 5 вопросов
- Тест на тему Когда появились первые известия о русских и Руси? 5 вопросов
- Тест на тему Призвание на княжение в Новгород варягов 5 вопросов
- Тест на тему История присоединения Псковского княжества к Московскому 5 вопросов
- Тест на тему История битв при Чашниках в 1564 и 1657 годах 5 вопросов
- Тест на тему Правление Василия 1 Дмитриевича 5 вопросов
- Тест на тему Земская реформа Ивана Грозного 5 вопросов
- Тест на тему Все князья Московского княжества 5 вопросов
- Тест на тему Причины, ход восстания Тадеуша Костюшко и его итоги 5 вопросов
- Тест на тему Последствия Смутного времени в России 5 вопросов
- Тест на тему Главные реформы короля Священной Римской империи Иосифа 2 5 вопросов
- Тест на тему Состав и функции государева двора 5 вопросов
- Тест на тему Суть “дела Дрейфуса” и реакция общества 5 вопросов
- Тест на тему Деятельность партии монтаньяров во Франции 5 вопросов
- Тест на тему Традиции и обычаи украинского народа 5 вопросов
- Тест на тему Причины закрытия Японии в 17 веке и последствия 5 вопросов
- Тест на тему Подготовка и содержание генерального плана “Ост” 5 вопросов
- Тест на тему Тайны убийства Петра Столыпина 5 вопросов
- Тест на тему Отмена подушной подати на Руси 5 вопросов
- Тест на тему Период регентства Елены Глинской: события и реформы 5 вопросов
- Тест на тему Экономика России в годы Первой мировой войны 5 вопросов
- Тест на тему Битва при деревне Лесной 28 сентября 1708 года 5 вопросов
- Тест на тему 10 любопытных фактов про Рождество 5 вопросов
- Тест на тему 10 любопытных фактов про Новый год 5 вопросов
- Тест на тему История потешных полков Петра Первого 5 вопросов
- Тест на тему Образование и распад тушинского лагеря при Лжедмитрии II 5 вопросов
- Тест на тему Чем ведал и какие функции выполнял Разрядный приказ? 5 вопросов
- Тест на тему Задачи и направления внешней политики России в 16 веке 5 вопросов
- Тест на тему Установление и отмена бессрочного сыска беглых крестьян на Руси 5 вопросов
- Тест на тему История создания и деятельности Вольного экономического общества 5 вопросов
- Тест на тему Период правления Вещего Олега: внешняя и внутренняя политика 5 вопросов
- Тест на тему Правление и политика князя Игоря 5 вопросов
- Тест на тему Суть и последствия Нерчинского договора России с Китаем 1689 года 5 вопросов
- Тест на тему Причины, ход и итоги войны за польское наследство 1733-1735 гг. 5 вопросов
- Тест на тему Восстановление экономики СССР после Великой Отечественной Войны 5 вопросов
- Тест на тему Как и зачем были созданы полки иноземного строя 5 вопросов
- Тест на тему Создание стрелецких войск при Иване Грозном 5 вопросов
- Тест на тему Причины, ход событий и итоги выступления старообрядцев при Петре I 7 вопросов
- Тест на тему Как и почему началась Ливонская война: основные причины 5 вопросов
- Тест на тему Реферат по физкультуре на тему: «Здоровое питание» 5 вопросов
- Тест на тему История развития лыжного спорта в разных странах - классификация и интересные факты 6 вопросов
- Тест на тему Важность самоконтроля при занятиях спортом 5 вопросов
- Тест на тему Как выполняются прыжки через козла? 5 вопросов
- Тест на тему Что такое здоровый образ жизни? 5 вопросов
- Тест на тему Как правильно выполнять кувырки? 5 вопросов
- Тест на тему Развитие гибкости тела: упражнения и польза для тела 5 вопросов
- Тест на тему Виды и польза прыжков через скакалку 5 вопросов
- Тест на тему Какие есть зимние виды спорта? 5 вопросов
- Тест на тему Реферат на тему: “Гимнастика как вид спорта” 8 вопросов
- Тест на тему Реферат по физкультуре на тему “Футбол” 7 вопросов
- Тест на тему Реферат по физкультуре на тему: “Баскетбол - виды и лиги” 7 вопросов
- Тест на тему Реферат на тему «Лыжный спорт» 10 вопросов
- Тест на тему Реферат по физической культуре «Формы и виды закаливания» 10 вопросов
- Тест на тему Образ Шарикова в повести «Собачье сердце» М. Булгакова 5 вопросов
- Тест на тему Образы героев в повести «Невский проспект» Н. Гоголя 5 вопросов
- Тест на тему Московские главы в романе «Мастер и Маргарита» Булгакова 7 вопросов
- Тест на тему Описание образа бирюка из рассказа И. Тургенева 7 вопросов
- Тест на тему Образы героев в романе «Отцы и дети» И. Тургенева 7 вопросов
- Тест на тему Образы героев в повести «Котлован» А. Платонова 7 вопросов
- Тест на тему Образы героев в пьесе «Гроза» А. Островского 7 вопросов
- Тест на тему История создания повести Н. В. Гоголя “Шинель” 7 вопросов
- Тест на тему История создания сборника рассказов Тургенева “Записки охотника” 7 вопросов
- Тест на тему История создания повести "Муму" Ивана Тургенева 7 вопросов
- Тест на тему История создания стихотворения "Реквием" Анны Ахматовой 10 вопросов
- Тест на тему История создания повести Гоголя "Тарас Бульба" 10 вопросов
- Тест на тему История создания стихотворения Пушкина "Деревня" 6 вопросов
- Тест на тему История создания стихотворения М. Лермонтова “Нищий” 7 вопросов
- Тест на тему История создания стихотворения "Она сидела на полу" 7 вопросов
- Тест на тему История создания Пушкиным стихотворения "К морю" 6 вопросов
- Тест на тему История создания повести «Станционный смотритель» А. Пушкина 10 вопросов
- Тест на тему История создания «Оды на день восшествия» М. Ломоносова 7 вопросов
- Тест на тему Проект на тему: “Экономика родного края: Самарская область” 5 вопросов
- Тест на тему Как люди узнают о том, что было в прошлом? 5 вопросов
- Тест на тему Какие животные впадают в спячку зимой: объяснения зоологов 7 вопросов
- Тест на тему Сообщение по окружающему миру для 4 класса об острове Врангеля 5 вопросов
- Тест на тему Сообщение о морских обитателях - описание, виды и названия 7 вопросов
- Тест на тему Что нужно сдавать на бухгалтера? 5 вопросов
- Тест на тему Какие предметы нужно сдавать на пилота 5 вопросов
- Тест на тему Какие экзамены нужно сдавать на фотографа? 5 вопросов
- Тест на тему Какие предметы нужно сдавать на хореографа? 5 вопросов
- Тест на тему Какие предметы нужно сдавать на актера? 5 вопросов
- Тест на тему Какие предметы нужно сдавать на режиссера? 5 вопросов
- Тест на тему Что нужно сдавать на художника? 5 вопросов
- Тест на тему Что нужно сдавать для поступления на визажиста? 5 вопросов
- Тест на тему Какие экзамены нужно сдавать на полицейского? 5 вопросов
- Тест на тему Какие предметы нужно сдавать на фармацевта? 5 вопросов
- Тест на тему Какие предметы сдавать для поступления на врача? 5 вопросов
- Тест на тему Какие экзамены нужно сдавать на учителя 5 вопросов
- Тест на тему Кадетский корпус - как поступить, чему учат и условия для проживания 5 вопросов
- Тест на тему Готовы ли вы к поступлению на психолога? 5 вопросов
- Тест на тему Готовы ли вы к поступлению на дизайнера? 5 вопросов
- Тест на тему Уровень урбанизации Африки: города растут, вызовы множатся 5 вопросов
- Тест на тему Уровень и особенности урбанизации Канады 5 вопросов
- Тест на тему Как найти полярную звезду и зачем ее искать? 5 вопросов
- Тест на тему Что нужно знать про контурные карты 5 вопросов
- Тест на тему Кто, когда и как открыл Австралию? 5 вопросов
- Тест на тему Характеристика природных зон Поволжья 5 вопросов
- Тест на тему Для каких рек в России характерно летнее половодье? 5 вопросов
- Тест на тему Как правильно заполнять дневник наблюдения за погодой 5 вопросов
- Тест на тему Влажные экваториальные леса - особенности климата, характеристика флоры и фауны 7 вопросов
- Тест на тему Европейский север России - географическое положение, особенности развития предприятий и промышленности 7 вопросов
- Тест на тему Что такое масштаб карты и как его определять 7 вопросов
- Тест на тему Особенности и примеры островных государств 5 вопросов
- Тест на тему Природные зоны Южной Америки - характеристики и особенности 7 вопросов
- Тест на тему 10 интересных фактов про океан 7 вопросов
- Тест на тему Сектор Газа: где он находится и откуда такое название? 6 вопросов
- Тест на тему Аргументы к сочинению ЕГЭ на тему: “Историческая память” 5 вопросов
- Тест на тему Аргументы для сочинения 9.3: Память сердца 5 вопросов
- Тест на тему Как правильно приводить аргументы в сочинении-рассуждении 5 вопросов
- Тест на тему Аргументы к сочинению на тему: «Добро и зло в пьесе “Гроза” А. Островского» 5 вопросов
- Тест на тему Аргументы к сочинению 15.3 из пьесы «Горе от ума» 5 вопросов
- Тест на тему Аргументы к итоговому сочинению по рассказу «Матренин двор» А. Солженицына 5 вопросов
- Тест на тему Аргументы для итогового сочинения ЕГЭ по роману «Мастер и Маргарита» 5 вопросов
- Тест на тему Особенности раздельного написания местоимений с предлогами 5 вопросов
- Тест на тему Правописание падежных окончаний прилагательных 5 вопросов
- Тест на тему Правописание слов с непроверяемой безударной гласной в корне 5 вопросов
- Тест на тему Нужно ли ставить запятую к фразе - "с уважением"? 5 вопросов
- Тест на тему «Во-вторых» или «во вторых» – как правильно пишется? 5 вопросов
- Тест на тему "Нету" или "нет" - как правильно писать и говорить? 5 вопросов
- Тест на тему «Не я» или «нея» – как правильно пишется? 5 вопросов
- Тест на тему «Полным-полно» или «полным полно» - как правильно пишется? 5 вопросов
- Тест на тему Как пишется «кто-нибудь» или «кто нибудь»? 5 вопросов
- Тест на тему Мягкий знак после шипящих в глаголах - правила, примеры 5 вопросов
- Тест на тему «Потвёрже» или «по твёрже» – как правильно пишется? 5 вопросов
- Тест на тему «Какой-то» или «какой то» – как пишется правильно? 5 вопросов
- Тест на тему «Мало-помалу» или «мало помалу» – как правильно пишется? 5 вопросов
- Тест на тему «По-осеннему» или «по осеннему» – как правильно пишется? 5 вопросов
- Тест на тему "Находу" или "на ходу" - слитно или раздельно писать? 5 вопросов
- Тест на тему "ЮлИчка" или "ЮлЕчка" - как правильно писать? 5 вопросов
- Тест на тему «Не пойму» или «непойму» – как правильно пишется? 5 вопросов
- Тест на тему «Доброе утро» − как правильно пишется? 5 вопросов
- Тест на тему «Почему-то» или «почему то» – как правильно пишется? 5 вопросов
- Тест на тему «На вынос» или «навынос» – как правильно пишется? 5 вопросов
- Тест на тему «Невежливо» или «не вежливо» – как правильно пишется? 5 вопросов
- Тест на тему «Негодуя» или «не годуя» - как правильно пишется? 5 вопросов
- Тест на тему «КуриНый» или «куриННый» − как правильно пишется? 5 вопросов
- Тест на тему «ТеННис» или «теНис» – как правильно пишется? 5 вопросов
- Тест на тему «ТумаННый» или «тумаНый» – как правильно пишется? 5 вопросов
- Тест на тему «ЗамечеННый» или «замечеНый» – как правильно пишется? 5 вопросов
- Тест на тему «Семнадцать» или «семЬнадцать» – как правильно пишется? 5 вопросов
- Тест на тему «ВыздОравливающий» или «выздАравливающий» – как правильно пишется? 5 вопросов
- Тест на тему «Свеж» или «свежЬ» – как правильно пишется? 5 вопросов
- Тест на тему «СлаЩе» или «слаДЧе» – как правильно пишется? 5 вопросов
- Тест на тему «ПрЕтерпевать» или «прИтерпевать» - как правильно пишется? 5 вопросов
- Тест на тему «Удастся» или «удастЬся» – как правильно пишется? 5 вопросов
- Тест на тему «СписаНо» или «СписаННо» – как правильно пишется? 5 вопросов
- Тест на тему «Происшествие» или «проишествие» – как правильно пишется? 5 вопросов
- Тест на тему «НачИнающий» или «начЕнающий» – как правильно пишется? 5 вопросов
- Тест на тему «Невозможно» или «не возможно» – как пишется слитно или раздельно? 5 вопросов
- Тест на тему «Налету» или «на лету» – как правильно пишется? 5 вопросов
- Тест на тему «Надолго» или «на долго» – как правильно пишется? 5 вопросов
- Тест на тему «ПьющАя» или «пьющЕя» – как правильно пишется? 5 вопросов
- Тест на тему «Неужели» или «не ужели» − как правильно пишется? 5 вопросов
- Тест на тему «НИкого» или «нЕкого» – как правильно пишется? 5 вопросов
- Тест на тему «БаССейн» или «баСейн» − как правильно пишется? 5 вопросов
- Тест на тему "Не согласованно" или "несогласованно" - слитно или раздельно? 5 вопросов
- Тест на тему «ОбстОятельствам» или «обстАятельствам» – как правильно пишется? 5 вопросов
- Тест на тему «ОбижеННый» или «обижеНый» – как правильно пишется? 5 вопросов
- Тест на тему «Аллах» или «Алах» – как правильно пишется? 5 вопросов
- Тест на тему «БелОрусский» или «белАрусский» – как правильно пишется? 5 вопросов
- Тест на тему «ЧИсло» или «чЕсло» – как правильно пишется? 5 вопросов
- Тест на тему «УвЕряющий» или «увИряющий» – как правильно пишется? 5 вопросов
- Тест на тему «НенасТный» или «ненасный» – как правильно пишется? 5 вопросов
- Тест на тему Анализ стихотворения “Каким бы малым ни был...” К. Кулиева 5 вопросов
- Тест на тему Анализ стихотворения «Цицерон» Ф. Тютчева 5 вопросов
- Тест на тему Анализ стихотворения “Поэт” М. Лермонтова 5 вопросов
- Тест на тему Анализ стихотворения “Пора, мой друг, пора” А. Пушкина 5 вопросов
- Тест на тему Анализ стихотворения «Шестое чувство» Н. Гумилева 5 вопросов
- Тест на тему Анализ стихотворения “Юбилейное” В. Маяковского 5 вопросов
- Тест на тему Анализ стихотворения “Мой гений” К. Батюшкова 5 вопросов
- Тест на тему Анализ стихотворения «Нет, не тебя так пылко» М. Лермонтова 5 вопросов
- Тест на тему Анализ стихотворения «Догорел апрельский светлый вечер…» И. Бунина 5 вопросов
- Тест на тему Анализ стихотворения «Фонтан» Ф. Тютчева 5 вопросов
- Тест на тему Анализ стихотворения «Посмотри - какая мгла» Я. Полонского 5 вопросов
- Тест на тему Анализ стихотворения «Школьник» Н. Некрасова 5 вопросов
- Тест на тему Анализ стихотворения «Несжатая полоса» Н. Некрасова 5 вопросов
- Тест на тему «Весенний дождь» - анализ стихотворения А.А. Фета 7 вопросов
- Тест на тему «Поет зима - аукает» - анализ стихотворения С.А. Есенина 7 вопросов
- Тест на тему Краткое содержание повести «А тем временем где-то» А. Алексина 5 вопросов
- Тест на тему Краткое содержание комедии «Мнимый больной» Жана-Батиста Мольера 5 вопросов
- Тест на тему Краткое содержание комедии “Доходное место” А. Островского 5 вопросов
- Тест на тему Краткое содержание новеллы “Падение дома Ашеров” Эдгара По 5 вопросов
- Тест на тему Краткое содержание рассказа “Крепкий мужик” В. Шукшина 5 вопросов
- Тест на тему Краткое содержание пьесы «Золотая карета» Л. Леонова 5 вопросов
- Тест на тему Краткое содержание рассказа «Когда в доме одиноко» К. Саймака 5 вопросов
- Тест на тему Краткое содержание рассказа “Простите нас” Ю. Бондарева 5 вопросов
- Тест на тему Краткое содержание романа “Кысь” Т. Толстой 5 вопросов
- Тест на тему Краткое содержание повести “Это мы, Господи!” К. Воробьева 5 вопросов
- Тест на тему Краткое содержание романа «Как закалялась сталь» Н. Островского 5 вопросов
- Тест на тему Краткое содержание романа-эпопеи «Хождение по мукам» А. Толстого 5 вопросов
- Тест на тему Краткое содержание сказки “Журавль и цапля” 5 вопросов
- Тест на тему Краткий пересказ “О чем говорят цветы” Жорж Санд 5 вопросов
- Тест на тему Краткое содержание рассказа “Тринадцать лет” С. Баруздина 5 вопросов
- Тест на тему Краткое содержание рассказа «Парадокс» В. Короленко 5 вопросов
- Тест на тему Краткое содержание романа «Живые и мертвые» К. Симонова 5 вопросов
- Тест на тему Краткое содержание повести «Обмен» Юрия Трифонова 5 вопросов
- Тест на тему Краткое содержание рассказа “Алешкино сердце” М. Шолохова 5 вопросов
- Тест на тему Краткое содержание рассказа “Как я стал писателем” И. Шмелева 5 вопросов
- Тест на тему Краткое содержание рассказа “Гамбринус” А. Куприна 5 вопросов
- Тест на тему Краткое содержание сказки “Вафельное сердце” Марии Парр 5 вопросов
- Тест на тему Краткое содержание рассказа “Специалист” А. Аверченко 5 вопросов
- Тест на тему Краткое содержание пьесы «Трамвай “Желание”» Т. Уильямса 5 вопросов
- Тест на тему Краткое содержание романа “Война миров” Г. Уэллса 5 вопросов
- Тест на тему Краткое содержание рассказа “Баргамот и Гараська” Л. Андреева 5 вопросов
- Тест на тему Краткое содержание повести “Скотный двор” Д. Оруэлла 5 вопросов
- Тест на тему «Акула» Л. Толстого - краткое содержание 5 вопросов
- Тест на тему Русская народная сказка «Хвосты» - краткое содержание 5 вопросов
- Тест на тему Краткое содержание оперы «Снегурочка» Римского-Корсакова 5 вопросов
- Тест на тему «Обезьяний язык» М. Зощенко – краткое содержание 10 вопросов
- Тест на тему «Сердце не камень» - краткое содержание пьесы А.Н. Островского 5 вопросов
- Тест на тему Балет «Щелкунчик» — краткое содержание 7 вопросов
- Тест на тему Биография Владимира Вольфовича Жириновского 5 вопросов
- Тест на тему Биография поэта и писателя Льва Рубинштейна 5 вопросов
- Тест на тему Биография президента Белоруссии Александра Лукашенко 5 вопросов
- Тест на тему 10 интересных фактов про Афанасия Фета 5 вопросов
- Тест на тему 10 интересных фактов про Ивана Тургенева 5 вопросов
- Тест на тему Биография писателя и поэта Вячеслава Урюпина 5 вопросов
- Тест на тему Биография поэта Николая Михайловича Рубцова 5 вопросов
- Тест на тему Биография поэта Андрея Дмитриевича Дементьева 5 вопросов
- Тест на тему Биография президента РФ Владимира Путина 5 вопросов
- Тест на тему Биография и личная жизнь Даниила Хармса 5 вопросов
- Тест на тему Краткая биография Валентины Осеевой 5 вопросов
- Тест на тему Григорий Остер: биография писателя и избранные произведения 7 вопросов
- Тест на тему Елена Благинина: творческая биография и личная жизнь 10 вопросов
- Тест на тему Биография детской писательницы Ирины Пивоваровой 5 вопросов
- Тест на тему История создания рассказа «Матренин двор» А. Солженицына 5 вопросов
- Тест на тему История создания песни «Смуглянка» 5 вопросов
- Тест на тему История создания поэмы “Кому на Руси жить хорошо” Н. Некрасова 5 вопросов
- Тест на тему История создания романа “Как закалялась сталь” Н. Островского 5 вопросов
- Тест на тему История создания оперы М. Глинки «Иван Сусанин» 5 вопросов
- Тест на тему История создания знаменитой песни “Катюша” 5 вопросов
- Тест на тему История создания поэмы “За далью - даль” А. Твардовского 5 вопросов
- Тест на тему История создания стихотворения “Смерть поэта” М. Лермонтова 5 вопросов
- Тест на тему История создания рассказа “Кавказский пленник” Л. Н. Толстого 5 вопросов
- Тест на тему История создания песни Р. Гамзатова “Журавли” 5 вопросов
- Тест на тему История создания стихотворения “Зимнее утро” А. С. Пушкина 5 вопросов
- Тест на тему История создания рассказа "Судьба человека" М. Шолохова 5 вопросов
- Тест на тему История создания стихотворения "На холмах Грузии лежит ночная мгла..." А. Пушкина 5 вопросов
- Тест на тему История создания романа “Идиот” Ф. М. Достоевского 5 вопросов
- Тест на тему История создания рассказа «Васюткино озеро» В. Астафьева 5 вопросов
- Тест на тему История создания повести “Детство” Л. Толстого 5 вопросов
- Тест на тему История создания романа «Дон Кихот» М. Сервантеса 5 вопросов
- Тест на тему История создания романа «Бесы» Ф. Достоевского 5 вопросов
- Тест на тему История создания романа «Молодая гвардия» А. Фадеева 5 вопросов
- Тест на тему История создания пьесы «Моцарт и Сальери» А. С. Пушкина 5 вопросов
- Тест на тему История создания баллады «Лесной царь» Ф. Шуберта 5 вопросов
- Тест на тему "Миссия русской эмиграции" И. Бунина 5 вопросов
- Тест на тему История создания пьесы «Бесприданниц» А. Островского 5 вопросов
- Тест на тему История создания повести “Алые паруса” А. Грина 1 вопрос
- Тест на тему История создания романа “Бедные люди” Ф. Достоевского 5 вопросов
- Тест на тему Герои романа “Властелин колец” Д. Толкина 5 вопросов
- Тест на тему Анализ сказа “Серебряное копытце” П. Бажова 5 вопросов
- Тест на тему Характеристика Дуняши в романе “Тихий Дон” М. Шолохова 5 вопросов
- Тест на тему Описание образа Фамусова - персонажа комедии “Горе от ума” 5 вопросов
- Тест на тему Характеристика образа Сатина - персонажа пьесы “На дне” М. Горького 5 вопросов
- Тест на тему Анализ повести “Сашка” В. Кондратьева 5 вопросов
- Тест на тему Характеристика образа Фауста из трагедии Гёте 9 вопросов
- Тест на тему Анализ романа “Портрет Дориана Грея” О. Уайльда 5 вопросов
- Тест на тему Характеристика колобка - героя русской народной сказки 5 вопросов
- Тест на тему Образ главной героини “Алисы в стране чудес” Л. Кэррола 5 вопросов
- Тест на тему Трактовки образа Иисуса Христа в поэме “Двенадцать” А. Блока 5 вопросов
- Тест на тему Образ Настеньки из повести “Белые ночи” Ф. Достоевского 5 вопросов
- Тест на тему Конфликт в рассказе “После бала” Л. Толстого 5 вопросов
- Тест на тему Образ главной героини повести “Бедная Лиза” Н. Карамзина 5 вопросов
- Тест на тему Описание образа Васютки из рассказа “Васюткино озеро” В. Астафьева 5 вопросов
- Тест на тему Образы чиновников в комедии “Ревизор” Н. Гоголя 5 вопросов
- Тест на тему Роль образа вишневого сада в пьесе А. Чехова 5 вопросов
- Тест на тему Характеристика профессора Преображенского в повести “Собачье сердце” М. Булгакова 5 вопросов
- Тест на тему Описание образа городничего в комедии “Ревизор” Н. Гоголя 5 вопросов
- Тест на тему Описание образа главного героя “Доктора Живаго” Б. Пастернака 5 вопросов
- Тест на тему Образ Цыганка в повести “Детство” М. Горького 5 вопросов
- Тест на тему Характеристика Вани Солнцева в повести “Сын полка” В. Катаева 5 вопросов
- Тест на тему Образ автора в поэме "Василий Теркин" А. Твардовского 5 вопросов
- Тест на тему Образ портрета в повести "Портрет" Н. В. Гоголя 5 вопросов
- Тест на тему Описание образа девушки-ундины из “Героя нашего времени” М. Лермонтова 5 вопросов
- Тест на тему Как выполнить разбор наречия по составу 5 вопросов
- Тест на тему Правила правописания суффиксов наречий 5 вопросов
- Тест на тему Морфологический признак наречий: неизменяемость 5 вопросов
- Тест на тему Чем отличаются и как найти тему и рему в тексте? 5 вопросов
- Тест на тему Способы и примеры образования наречий 5 вопросов
- Тест на тему Особенности и применение составных предлогов 5 вопросов
- Тест на тему Какую синтаксическую роль в предложении выполняет наречие 5 вопросов
- Тест на тему Какие признаки прилагательного есть у причастия 5 вопросов
- Тест на тему Морфологический разбор союзов: инструкция, примеры 5 вопросов
- Тест на тему Морфологические признаки действительных и страдательных причастий 5 вопросов
- Тест на тему Особенности и примеры звукоподражательных слов 5 вопросов
- Тест на тему Какие бывают и как определить смысловую группу наречий 5 вопросов
- Тест на тему Неправильное построение предложений с косвенной речью: примеры ошибок 5 вопросов
- Тест на тему Расстановка знаков препинания в сложноподчиненных предложениях 5 вопросов
- Тест на тему Виды синтаксических связей в словосочетаниях и предложениях 5 вопросов
- Тест на тему Оформление и примеры несобственно-прямой речи в тексте 5 вопросов
- Тест на тему Структура текста с параллельной связью предложений 5 вопросов
- Тест на тему Литературный язык: понятие, признаки, формы 5 вопросов
- Тест на тему Функции и роль языка в жизни человека и общества 5 вопросов
- Тест на тему Сообщение на тему: «Традиции русской речевой манеры общения» 5 вопросов
- Тест на тему Определение и виды простых осложненных предложений 5 вопросов
- Тест на тему Какие бывают виды текстов? 5 вопросов
- Тест на тему Образование и правописание страдательных причастий настоящего времени 5 вопросов
- Тест на тему Как определить начальную форму прилагательного? 5 вопросов
- Тест на тему Местоимение-прилагательное в русском языке 5 вопросов
- Тест на тему Сборник правил по русскому языку для 6 класса 7 вопросов
- Тест на тему Сборник правил по русскому языку за 5 класс 7 вопросов
- Тест на тему Упражнения для тренировки школьников 7 класса по причастному обороту 9 вопросов
- Тест на тему Тест: Склонение фамилий в русском языке 7 вопросов
- Тест на тему Общеупотребительные и необщеупотребительные слова 5 вопросов
- Тест на тему Дефисное и слитное написание сложных прилагательных 5 вопросов
- Тест на тему Морфологический разбор числительного - правило и примеры 5 вопросов
- Тест на тему "Банты" - как правильно ставить ударение в слове? 5 вопросов
- Тест на тему «Конечно же» - выделяется ли слово запятыми? 5 вопросов
- Тест на тему «Подчеркивать» – как правильно ставить ударение в слове? 5 вопросов
- Тест на тему «Лифты» – как правильно ставить ударение в слове? 5 вопросов
- Тест на тему «Строку» – как правильно ставить ударение в слове? 5 вопросов
- Тест на тему «Апостроф» – как правильно ставить ударение в слове? 5 вопросов
- Тест на тему «Зубчатый» – как правильно ставить ударение в слове? 5 вопросов
- Тест на тему «Прозорлива» – как правильно ставить ударение в слове? 5 вопросов
- Тест на тему «Балашиха» – как правильно ставить ударение в слове? 5 вопросов
- Тест на тему «Реку» – как правильно ставить ударение в слове? 5 вопросов
- Тест на тему «Полно» – как правильно ставить ударение в слове? 5 вопросов
- Тест на тему «Говорено» – как правильно ставить ударение в слове? 5 вопросов
- Тест на тему «Досыта» – как правильно ставить ударение в слове? 5 вопросов
- Тест на тему «Упрочение» – как правильно ставить ударение в слове? 5 вопросов
- Тест на тему «Развила» – как правильно ставить ударение в слове? 5 вопросов
- Тест на тему «Подолгу» – как правильно ставить ударение в слове? 5 вопросов
- Тест на тему «Логин» – как правильно ставить ударение в слове? 5 вопросов
- Тест на тему «Окон» – как правильно ставить ударение в слове? 5 вопросов
- Тест на тему «Втридорога» – как правильно ставить ударение в слове? 5 вопросов
- Тест на тему «Утра» – как правильно ставить ударение в слове? 5 вопросов
- Тест на тему «Запломбированный» – как правильно ставить ударение в слове? 5 вопросов
- Тест на тему «Цыган» – как правильно ставить ударение в слове? 5 вопросов
- Тест на тему «Шарфы» – как правильно ставить ударение в слове? 5 вопросов
- Тест на тему «Бармен» – как правильно ставить ударение в слове? 5 вопросов
- Тест на тему «Положенный» – как правильно ставить ударение в слове? 5 вопросов
- Тест на тему «Крадущийся» – как правильно ставить ударение в слове? 5 вопросов
- Тест на тему «Донизу» – как правильно ставить ударение в слове? 5 вопросов
- Тест на тему «Явишься» – как правильно ставить ударение в слове? 5 вопросов
- Тест на тему «Ободрить» - как правильно ставить ударение в слове? 5 вопросов