Виды и режимы термической обработки стали
Пластичность стали, столь необходимая при формоизменяющей обработке заготовок, часто превращается в негативный фактор: в частности, производство не устраивают невысокая твёрдость и прочность продукции, пусть даже и увеличивающиеся вследствие деформационного упрочнения. Проблему решает термическая обработка стали.
Благодаря множеству различных процессов термообработки свойства стали могут быть значительно изменены как по физическим, так и по и механическим характеристикам. Термической обработке можно подвергать преобладающее большинство марок чёрных и цветных металлов и сплавов.
Задачи и эффекты термообработки
При нагреве до температур, превышающих температуру рекристаллизации, микроструктура большинства марок сталей становится равновесной, а свойства – более равномерными во всех направлениях. Однако при естественном охлаждении такие преимущества не сохраняются. Более того, образуются грубые кристаллиты, возрастает полосчатость и иные дефекты, ухудшающие эксплуатационные свойства металла.
Для сохранения положительных характеристик было бы удобно зафиксировать при комнатных температурах благоприятные фазово-структурные изменения. Самый простой способ – нагреть изделие до нужной температуры, а затем быстро его охладить. На этом принципе построено большинство технологий термообработки.
Когда мы говорим об изменении механических свойств, то имеем в виду прочность на сдвиг, ударную вязкость предел прочности и твёрдость стали. Учет такого механического изменения свойств позволяет коечной продукции быть более эффективной при выполнении повседневных задач и более устойчивой к износу даже в самых тяжелых условиях. Правильная термообработка стали снижает трудоёмкость других важных этапов производства. Например, в результате разумно использованных возможностей процессов термообработки можно снять напряжения, облегчая сборку или сварку конструктивных элементов, а также оптимизировать размеры их сечений.
Шестерни, валы, подшипники и другие важные компоненты машиностроительных узлов значительно выигрывают от таких процессов термообработки, когда увеличивается их износостойкость и общий срок службы. В частности, повышение усталостной прочности позволяет стальным изделиям более эффективно сопротивляться знакопеременным и ударным нагрузкам.
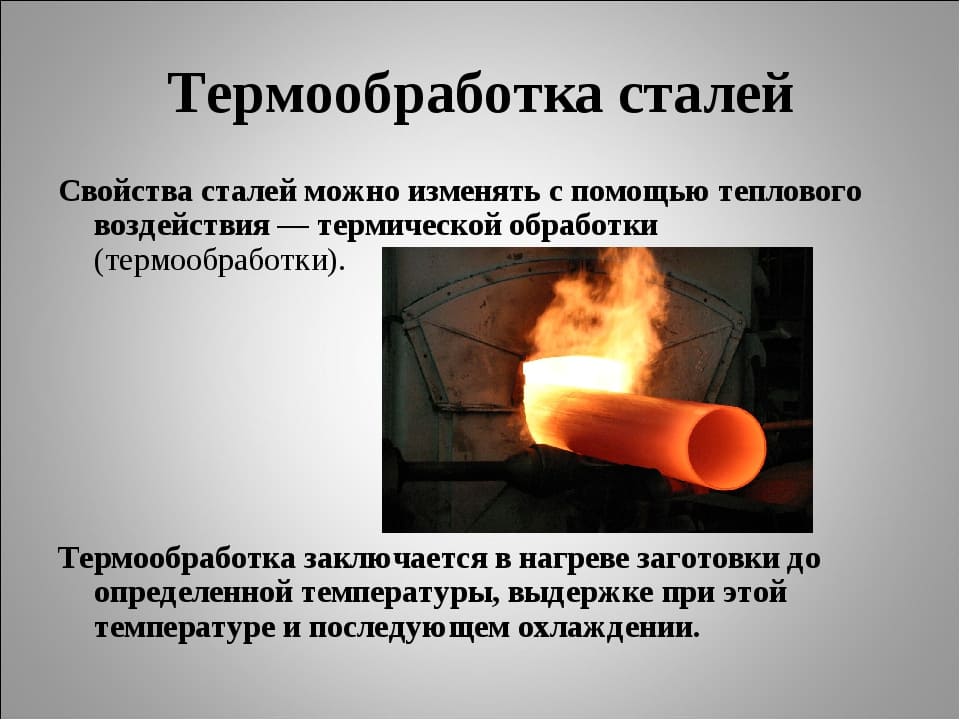
Велика роль процессов термообработки и в инструментальном производстве. Твёрдые стали и сплавы часто используются в качестве режущих и штамповых деталей, где необходимо поддерживать четкость формы и кромки. При этом можно достигать требуемого баланса между поверхностными твёрдыми слоями инструмента и более вязкой, пластичной сердцевиной.
Суммируя, можно отметить, что в результате термической обработки материал:
- Становится более прочным и твёрдым (или, наоборот, более мягким и пластичным!);
- Повышает свою усталостную прочность;
- Улучшает свариваемость;
- Обеспечивает необходимую микроструктуру;
- В ряде случаев изменяет химический состав поверхности.
Во многих случаях термообработка обратима, что позволяет изменять свойства стали, если по каким-либо причинам полученные характеристики не удовлетворяют производственным требованиям.
Принцип термической обработки металлов
Результаты, которые могут быть получены при термической обработке, в значительной степени зависят от структуры металла и того, как структура изменяется при нагревании и охлаждении металла. Для чистых металлов термическая обработка малоэффективна, поскольку при нагревании их структура мало изменяется. С другой стороны, большинство сплавов поддаются термической обработке именно потому, что их структура изменяется в процессе нагревания и охлаждения.
Исходный сплав может находиться в следующих формах:
- Твёрдого раствора;
- Механической смеси;
- Комбинации твёрдого раствора и механической смеси.
Когда сплав находится в форме твёрдого раствора, элементы и соединения, образующие сплав, растворяются один в другом, почти так же, как соль растворяется в стакане воды. Составные части не могут быть идентифицированы даже под микроскопом. Когда два или более элемента или соединения смешиваются, но могут быть идентифицированы с помощью микроскопического исследования, образуется механическая смесь.
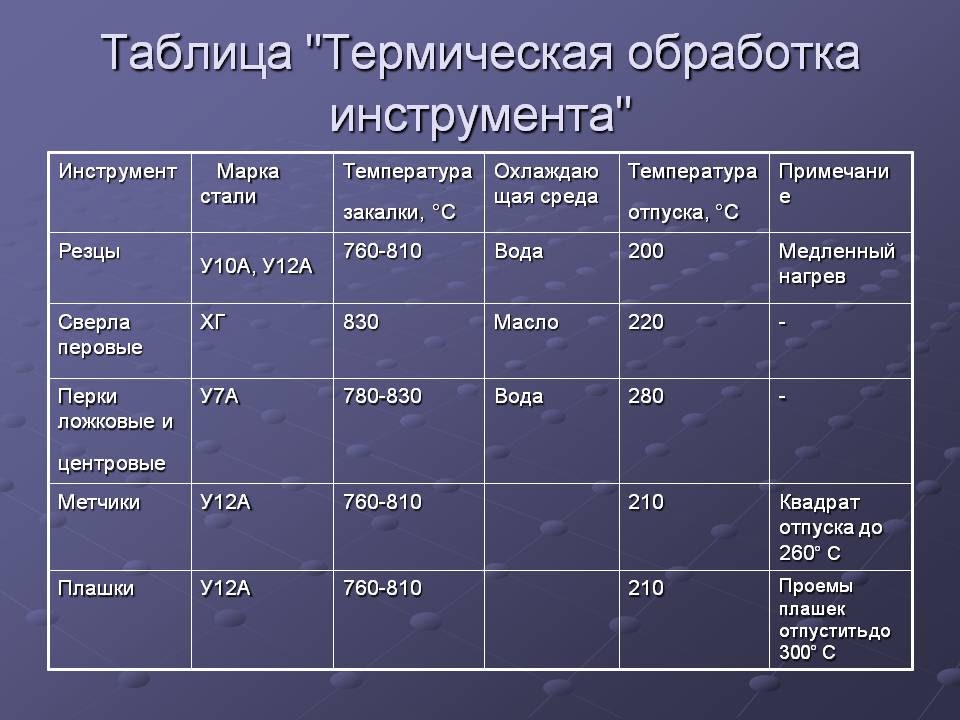
Механическую смесь можно сравнить со смесью песка и гравия в бетоне, когда отчётливо видны и песок, и гравий. Подобно тому, как песок и гравий удерживаются вместе смесью цемента, так и другие составляющие сплава погружаются в смесь, образованную основным металлом.
Сплав, который находится в виде механической смеси при обычных температурах, может превращаться в твёрдый раствор при нагревании. При охлаждении до нормальной температуры сплав может вернуться к своей исходной структуре. Вместе с тем, он может оставаться твёрдым раствором или образовывать комбинацию твёрдого раствора и механической смеси.
Сплав, состоящий из комбинации твёрдого раствора и механической смеси при нормальных температурах, может превратиться в твёрдый раствор при нагревании. При охлаждении сплав может оставаться твёрдым раствором, возвращаться к своей первоначальной структуре или образовывать сложный раствор.
Таким образом, все виды термической обработки стали представляются цепочкой взаимосвязанных событий/циклов. Эти циклы включают:
- Нагрев (обычно медленный, для того, чтобы обеспечить структурную равномерность);
- Выдержку металла при заданной температуре в течение определённого периода времени;
- Охлаждение (или возвращение) металла к комнатной температуре, иногда быстро, иногда медленно.
В цикле нагрева первостепенное значение имеет равномерность температур. Если одна часть детали нагревается быстрее, чем другая, возникающее в результате неравномерное расширение часто вызывает деформацию или растрескивание детали.
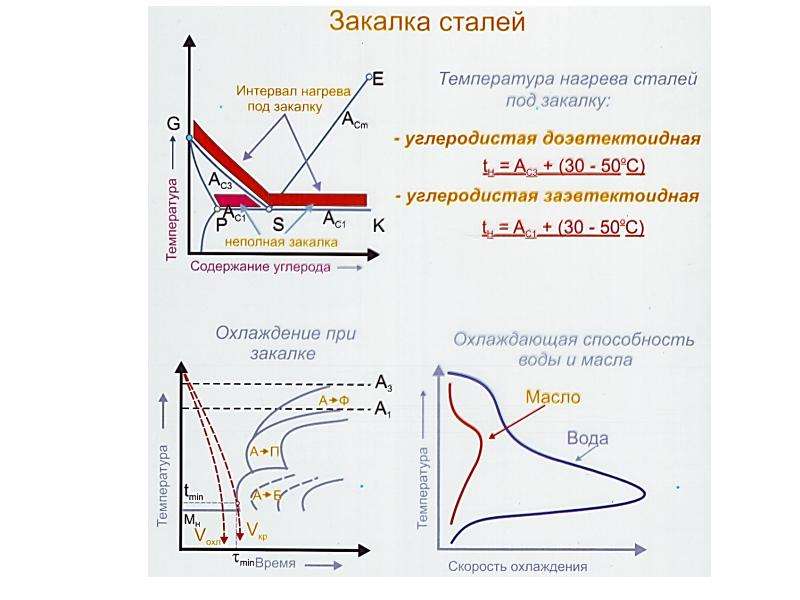
Скорость нагрева детали зависит от нескольких факторов. Одним из важных является теплопроводность металла. Металл, который легко проводит тепло, может нагреваться с большей скоростью, чем металл, при котором тепло не может быстро поглощается всей деталью. Состояние металла также влияет на скорость его нагрева. Например, скорость нагрева закалённых инструментов и деталей должна быть ниже, чем у металлов, не находящихся в напряженном состоянии.
Размер и поперечное сечение имеют важное влияние на скорость нагрева. Детали с развитым поперечным сечением требуют более медленного нагрева, чем тонкие детали. Эта необходимо для того, чтобы внутреннее пространство было нагрето до той же температуры, что и поверхность. Нагрев таких заготовок затруднён, зато они менее склонны к растрескиванию или чрезмерной деформации.
Целью термической обработки является изменение свойств металла. Для этого металл должен быть нагрет до температуры, при которой происходят внутренние структурные изменения. Эти изменения происходят, когда составляющие металла переходят в раствор. Однако каждый металл обладает свойством тепловой инерции. Это означает, что, после того, как металл нагреется до надлежащей температуры, его необходимо выдерживать при этой же температуре, пока металл не прогреется полностью.
Время выдержки зависит от химического состава металла и массы детали. Если стальные детали неоднородны по поперечному сечению, то время выдержки определяется самым большим сечением.
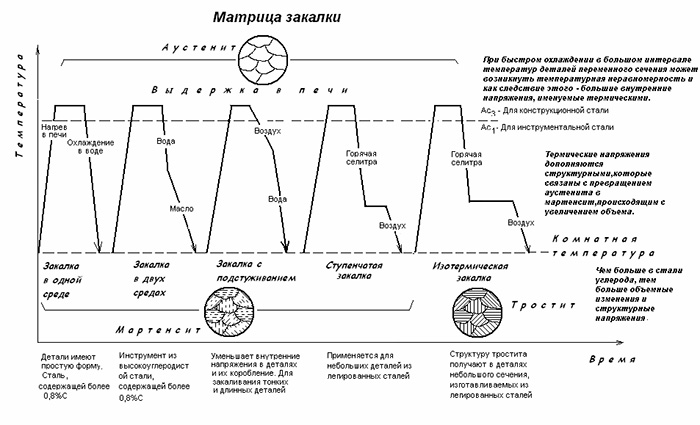
Температура металла редко повышается от комнатной до конечной за одну операцию. Поэтому сталь медленно нагревают до температуры ниже точки, при которой образуется твёрдый раствор, а затем выдерживают при этой температуре до тех пор, пока тепло не поглотится металлом. Эта стадия называется предварительным нагревом, после него нагрев можно вести быстрее. Предварительный нагрев способствует достижению равномерной температуры по всей детали, снижая риск деформации и растрескивания.
После нагрева до надлежащей температуры металл необходимо вернуть к комнатной температуре, завершив процесс термообработки. Металл охлаждается путем непосредственного контакта с газом, жидкостью или их сочетанием. Твердое, жидкое или газообразное вещество, используемое для охлаждения металла, называется «охлаждающей средой». Скорость охлаждения металла зависит от:
- Вида металла,
- Желаемых свойств;
- Характеристик охлаждающей среды.
Выбор охлаждающей среды имеет важное влияние на получаемые свойства. Чаще других используют масло и воду. Вода (и растворы на её основе) охлаждают быстрее и должны использоваться только для металлов, которые требуют быстрого охлаждения. Масло охлаждает медленнее и больше подходит для металлов, которые легко повредить при быстром охлаждении. Углеродистые стали чаще охлаждают в воде, а легированные стали - в масле.
Виды термообработки стали
Включают в себя отжиг, закалку, отпуск, термомеханическую и механо-термическую обработку, а также химико-термическую обработку и обработку холодом.
Отжиг
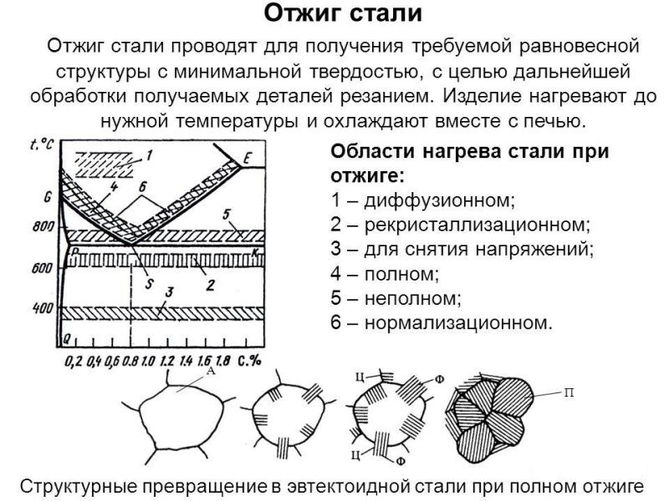
Операция отжига состоит в нагреве стали до заданной температуры, выдержки при этой температуре и в последующем медленном охлаждении (часто – вместе с печью). Главная цель отжига – получение равновесной структуры. Поэтому в процеесе отжига улучшаются механические свойства, выравнивается химический состав сталей, улучшается их обрабатываемость, уменьшаются остаточные деформации. Часто отжиг входит в число предварительных операций термообработки, в результате которой требуется подготовить исходную структуру к дальнейшим переходам. Отжиг подразделяют на:
- Рекристаллизационный, целью которого является снятие наклёпа;
- Полный или неполный – различаются степенью завершённости структурных перестроек;
- Сфероидизационный, который выполняется с целью получения структуры зернистого перлита;
- Изотермический, которому подвергают легированные стали;
- Низкотемпературный (для снятия внутренних напряжений);
- Диффузионный, при котором гарантируется наивысшая структурная однородность металла.
Конкретные температуры нагрева металла при отжиге зависят от марки стали.
Закалка
Режим термической обработки стали при закалке устанавливается по химсоставу и структуре стали. В зависимости от структуры различают доэвтектоидные и заэвтектоидные стали. После завершения процесса кристаллизации первые содержат не более 0,8 % С, вторые – более 0,8% С. В структуре доэвтектоидных сталей присутствуют феррит и перлит, в то время как структуру заэвтектоидных сталей представляют перлит и вторичный цементит Fe3C.
На типовой диаграмме состояния углеродистых сталей линия Ас3, которая определяет температурную границу аустенитного превращения, зависит от процентного содержания углерода. С увеличением этого содержания она снижается от 9000С (для малоуглеродистых сталей) до 7230С – для средне- и высокоуглеродистых.
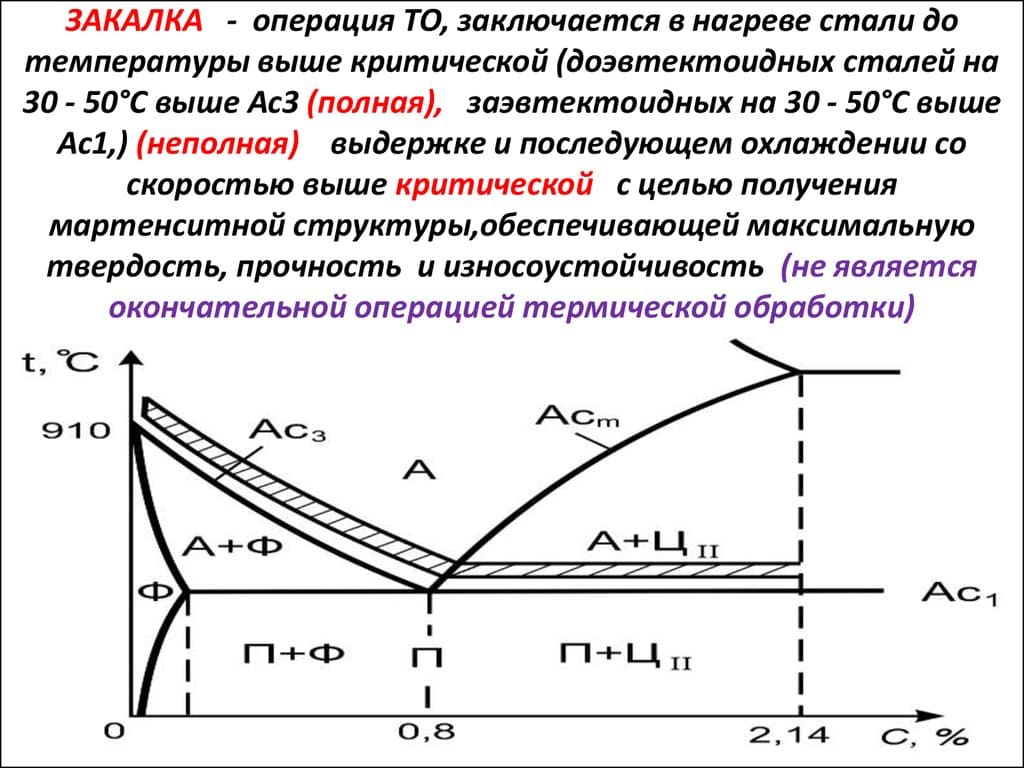
Доэвтектоидную сталь нагревают до температуры, на 20…300С превышающую линию Ас3, а заэвтектоидную – до температур, на 20…300С превышающих температуру точки Ас1.
В результате закалки в стали образуются неравновесные структуры, поскольку последующее быстрое охлаждение затрудняет любые фазовые превращения. Поэтому твёрдость (а, следовательно, и хрупкость) стали после закалки резко увеличивается. В структуре таких сталей присутствуют мартенсит, значительное количество не успевших раствориться карбидов, а также остаточный аустенит.
Закалку подразделяют на полную, неполную и изотермическую. Во многих случаях закалку ведут по ступенчатой схеме, многократно нагревая металл. В результате структурные изменения наблюдаются по всему сечению, с соответствующим превращением аустенита в мартенсит.
Сталь после закалки не может непосредственно использоваться для дальнейшей обработки, поэтому возникающие структурные напряжения приходится снимать последующим отпуском.
Отпуск
Представляет собой операцию нагрева и выдержки предварительно закалённой стали при температуре на 20…300С ниже критической точки начала мартенситного превращения. Как следствие, происходит частичное превращение остаточного аустенита и мартенсита, сопровождающееся снятием внутренних напряжений, снижением хрупкости, повышением вязкости и пластичности стали. Несколько снижается твёрдость металла.
Отпуску подвергают все предварительно закалённые детали, за исключением тех, которые прошли изотермическую закалку. Отпуск ведут в масляных средах, селитровых ваннах или в отпускных печах с принудительной циркуляцией воздуха.
Режимы отпуска определяются химическим составом и необходимыми показателями твёрдости стали.
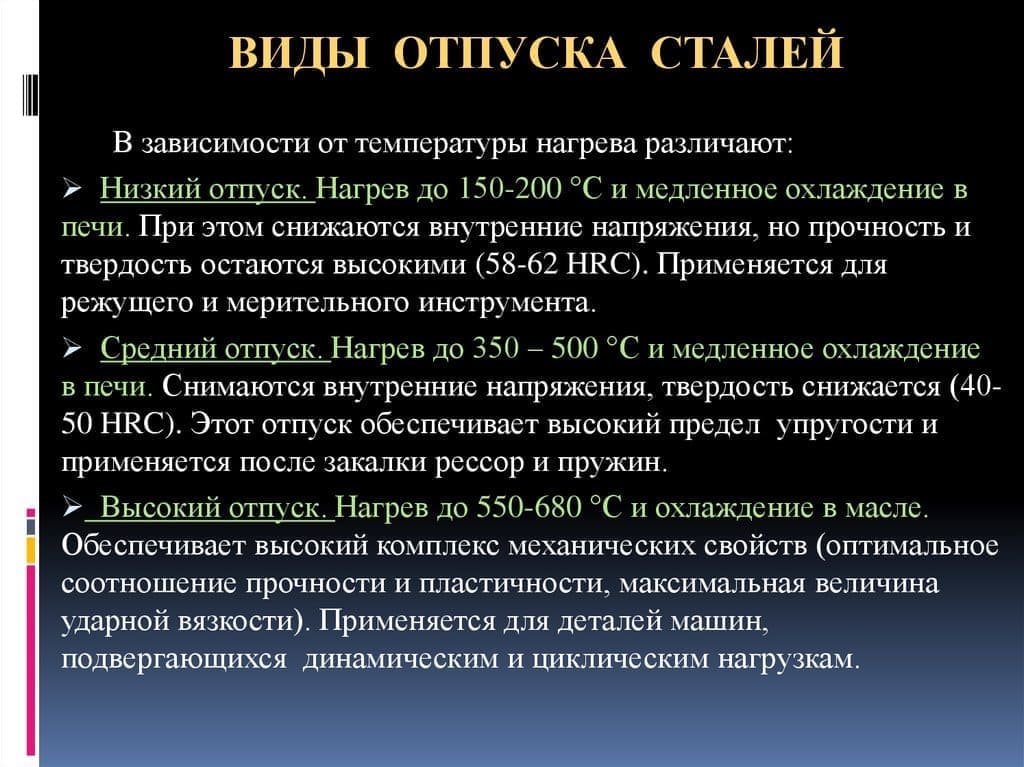
Химико-термическая обработка
Основное назначение термической обработки стали – изменение её структуры и твёрдости, однако в некоторых случаях требуется менять также и химический состав поверхностных и особенно – глубинных слоёв изделия. Эту функцию выполняют процессы химико-термической обработки.
Эти процессы различаются:
- Источниками получаемых изменений. Ими могут быть тепло, генерируемое нагретыми рабочими средами (газом, расплавами) и электроэнергией (в последнем случае отдельно выделяют технологии электро-химико-термической обработки;
- Материалами или соединениями, которые внедряются в исходную микроструктуру. По этому принципу отдельно рассматривают операции азотирования, борирования, цементирования, нитридирования (отличается от азотирования тем, что в структуре присутствует не сам азот, а его соединения), алюминирования, сульфидирования и т.д.
- Способами реализации: электрическом дуговым разрядом, электроисковым легированием, диффузионной металлизацией и пр.
По ряду причин химико-термическая обработка является наиболее универсальным, прогрессивным и точным методом желаемого изменения структуры и свойств термически обрабатываемой стали.
Термомеханическая обработка
Этот вид тепловой обработки сталей (как и родственная ему механо-термическая обработка) относится к числу комбинированных технологий. Она заключается в одновременном воздействии на металл высоких температур и пластических деформаций, которые ведутся в диапазонах структурных превращений. Эффективность способов обуславливается меньшим временем и более высокой однородностью происходящих структурных превращений.
Термомеханическая обработка применима не ко всем видам сталей.
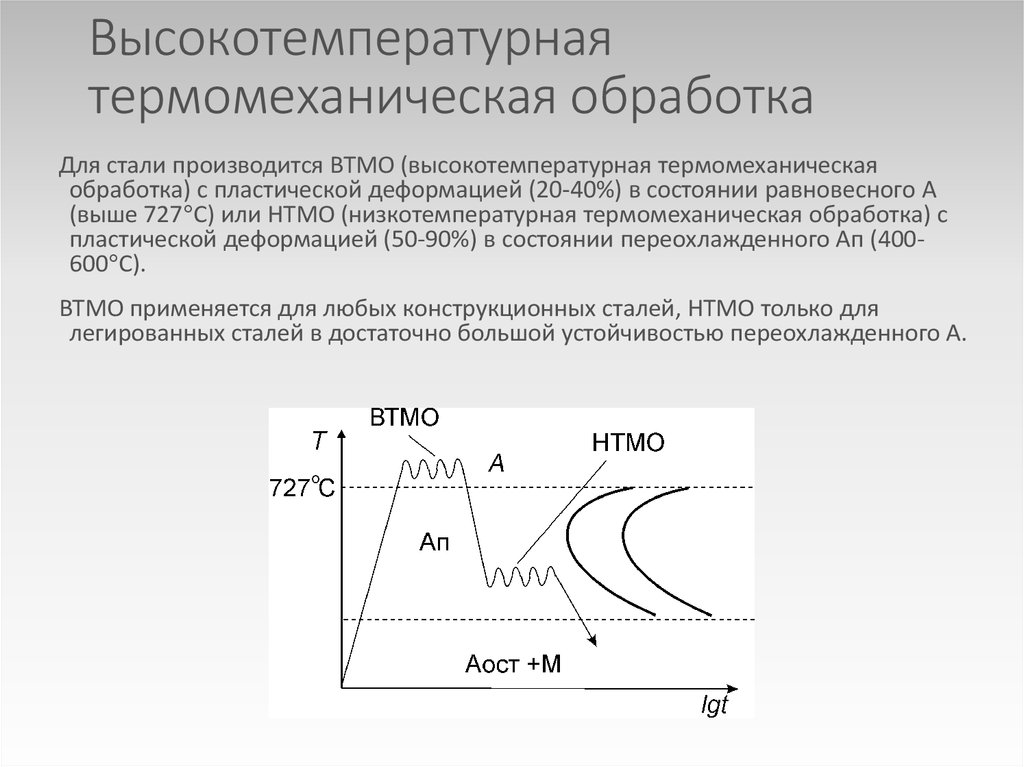
Криогенная обработка
Как ни парадоксально, но термообработка металлов может проводиться не только при повышенных, но и при пониженных температурах заготовок. Такие процессы называют также обработкой холодом.
Необходимость в криогенной обработке связана с тем, что в некоторых случаях отпуск закалённых сталей не приносит должного результата, поскольку количество нежелательного остаточного аустенита остаётся высоким. Применение криогенной обработки обеспечивает:
- Улучшение механических свойств сталей, особенно быстрорежущих;
- Повышение износостойкости контрольно-измерительных инструментов;
- Увеличение твёрдости нержавеющих сталей;
- Повышение качества поверхности, которая в дальнейшем будет подвергаться полировке.
Во всех случаях обработка холодом способствует стабилизации размеров заготовок.
Применяемое оборудование
Термические печи можно разделить на два основных типа: периодические и непрерывные. Принципиальная разница между ними заключаются в том, как обрабатываемые заготовки размещаются в агрегатах, и как они взаимодействуют с атмосферой внутри печей.
Основными источниками энергии для нагрева оборудования являются природный газ и электричество. Реже используются альтернативные источники энергии, например, мазут.
Печи, в которых ведётся термообработка металлов, классифицируются по верхнему пределу температуры нагрева. Обычно используемый температурный диапазон – от 600 до 8000С. Преимущественно применяется конвекционный нагрев, основанный на циркуляции воздуха, продуктов сгорания или инертного газа находящихся внутри печи.
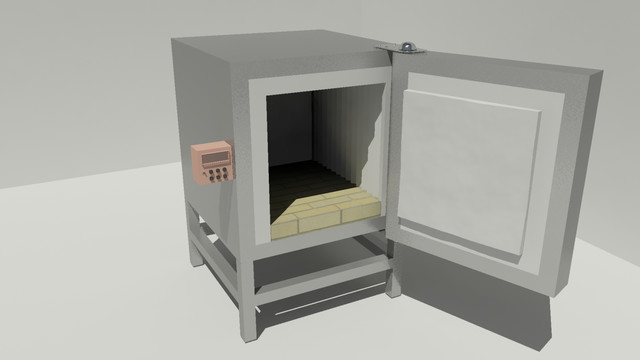
Установки периодического действия, как правило, обрабатывают заготовки партиями, причём нагрев каждой партии может продолжаться несколько часов (а иногда – и суток). В печи периодического действия рабочая загрузка обычно является стационарной, так что взаимодействие с изменениями в атмосфере печи осуществляется в условиях, близких к равновесным. Типы периодических печей:
- Колпаковые;
- Коробчатые;
- Нагревательные колодцы;
- С подвижным подом;
- С псевдоожиженным слоем;
- Шахтные;
- Вакуумные.
Печи непрерывного действия различаются способом движения обрабатываемых заготовок и характеристиками рабочей среды (воздух, инертный газ или вакуум).
Типы печей непрерывного действия:
- Камерные;
- Ленточные
- Монорельсовые
- Толкательные
- С роликовым/вращающимся подом;
- Печи с вибрирующим подом;
- Вакуумные печи;
- С шагающими балками.
Наилучшее регулирование параметрами нагрева обеспечивают электропечи.
Особенности термообработки цветных сплавов
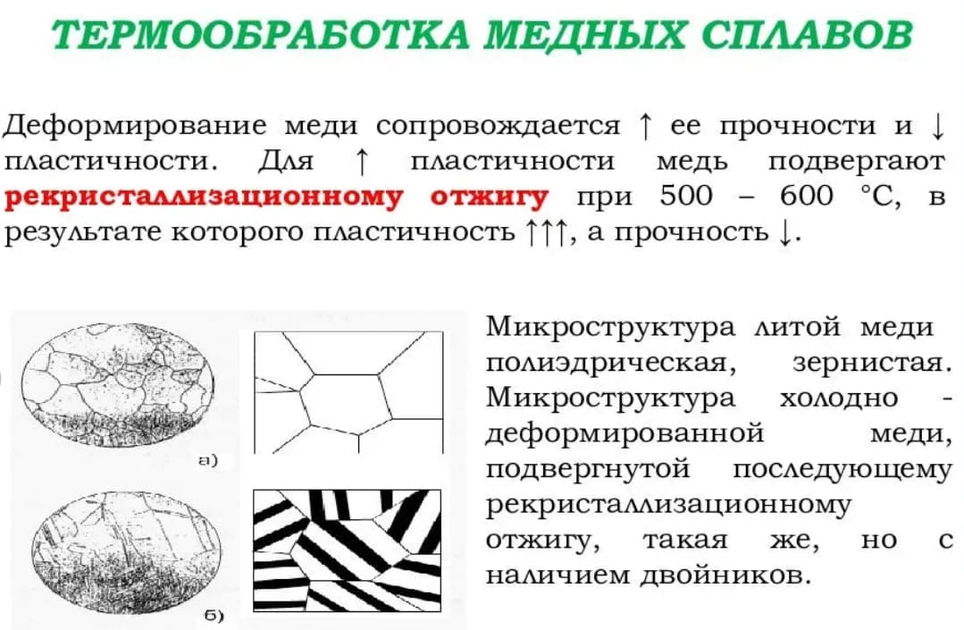
Большинство сплавов можно подвергать двум видам термообработки – закалке и старению. Последняя разновидность представляет собой отпуск, проводимый при температурах 120…2000С, с охлаждением при комнатной температуре (естественное старение) или с подачей воздушной струи (искусственное старение).
Однако существует большой разброс между многими комбинациями металлов и цветных сплавов по скорости деформационного упрочнения, что затрудняет систематизацию процессов термообработки цветных сплавов.
Основные особенности:
- Сплавы системы «медь-никель» эффективно поддаются механо-термической обработке, при которой структура становится мелкозернистой, но твёрдость повышается.
- Все виды цветных сплавов поддаются отжигу, при этом тип нагрева не имеет значения, поскольку интенсивность окалинообразования невысока. Меньшее влияние на эффективность отжига оказывает время, чем температура.
- Закалка цветных сплавов значительно менее эффективна. За исключением титана, широко используемые сплавы алюминия, меди и магния не являются аллотропными; таким образом, они не реагируют так же, как стали, при своём нагревании и охлаждении.
- Многие сплавы типа бронз термообработке вообще не поддаются, поскольку для этих сплавов твердые растворы, образующиеся при повышенной температуре, остаются полностью стабильными при комнатной температуре или ниже.
- Температурные и временные циклы термообработки охватывают широкий диапазон, который зависит не только от состава сплава, но и от того, находится ли сплав в деформируемом или литом состоянии.
Цветные металлы редко подвергаются предварительному нагреву, поскольку он приводит к увеличению размера зерна и ухудшает структуру сплава.
Все тесты
- Английский язык
- Биология
- Помощь студенту
- Пушкин А.С
- Религия
- Карьера
- Информатика
- Физика
- Стихи
- Обществознание
- Сочинения
- ОБЖ
- Экономика
- Физкультура
- Окружающий мир
- История
- Подготовка к ЕГЭ
- Математика
- Пунктуация
- Правоведение
- Орфография
- Анализ стихотворений
- Краткие содержания
- Биографии
- Литература
- Русский язык
- География
- Фонетический разбор
- Тест на тему To be going to: значение, правила употребления 5 вопросов
- Тест на тему Конструкция go on: значения, правила употребления, примеры 5 вопросов
- Тест на тему Be familiar with: значение и правила употребления 5 вопросов
- Тест на тему Британский vs американский английский: в чем разница? 5 вопросов
- Тест на тему Be mad about - как переводится и как использовать в речи 5 вопросов
- Тест на тему Be hooked on в английском языке: значение и примеры предложений 5 вопросов
- Тест на тему «To be made» в английском языке: значение, правила и примеры для школьников 5 вопросов
- Тест на тему Приставки in-, im-, il-, ir- в английском языке: полный разбор для школьников 5 вопросов
- Тест на тему «To be given» в английском языке: значение, употребление и примеры для школьников 5 вопросов
- Тест на тему Подборка интересных фактов про английский язык 5 вопросов
- Тест на тему История сибирской язвы и как она стала оружием 5 вопросов
- Тест на тему Что такое “железное легкое” и как жилось узникам аппарата 5 вопросов
- Тест на тему Суть и методы клеточной инженерии 5 вопросов
- Тест на тему Злаковые растения - общая характеристика, признаки и список представителей 7 вопросов
- Тест на тему Семейство бобовые - общая характеристика, строение и представители 7 вопросов
- Тест на тему Что нужно сдавать на бухгалтера? 5 вопросов
- Тест на тему Какие предметы нужно сдавать на пилота 5 вопросов
- Тест на тему Какие экзамены нужно сдавать на фотографа? 5 вопросов
- Тест на тему Какие предметы нужно сдавать на хореографа? 5 вопросов
- Тест на тему Какие предметы нужно сдавать на актера? 5 вопросов
- Тест на тему Какие предметы нужно сдавать на режиссера? 5 вопросов
- Тест на тему Что нужно сдавать на художника? 5 вопросов
- Тест на тему Что нужно сдавать для поступления на визажиста? 5 вопросов
- Тест на тему Какие экзамены нужно сдавать на полицейского? 5 вопросов
- Тест на тему Какие предметы нужно сдавать на фармацевта? 5 вопросов
- Тест на тему Какие предметы сдавать для поступления на врача? 5 вопросов
- Тест на тему Какие экзамены нужно сдавать на учителя 5 вопросов
- Тест на тему Кадетский корпус - как поступить, чему учат и условия для проживания 5 вопросов
- Тест на тему Готовы ли вы к поступлению на психолога? 5 вопросов
- Тест на тему Готовы ли вы к поступлению на дизайнера? 5 вопросов
- Тест на тему Образ Шарикова в повести «Собачье сердце» М. Булгакова 5 вопросов
- Тест на тему Образы героев в повести «Невский проспект» Н. Гоголя 5 вопросов
- Тест на тему Московские главы в романе «Мастер и Маргарита» Булгакова 7 вопросов
- Тест на тему Описание образа бирюка из рассказа И. Тургенева 7 вопросов
- Тест на тему Образы героев в романе «Отцы и дети» И. Тургенева 7 вопросов
- Тест на тему Образы героев в повести «Котлован» А. Платонова 7 вопросов
- Тест на тему Образы героев в пьесе «Гроза» А. Островского 7 вопросов
- Тест на тему История создания повести Н. В. Гоголя “Шинель” 7 вопросов
- Тест на тему История создания сборника рассказов Тургенева “Записки охотника” 7 вопросов
- Тест на тему История создания повести "Муму" Ивана Тургенева 7 вопросов
- Тест на тему История создания стихотворения "Реквием" Анны Ахматовой 10 вопросов
- Тест на тему История создания повести Гоголя "Тарас Бульба" 10 вопросов
- Тест на тему История создания стихотворения Пушкина "Деревня" 6 вопросов
- Тест на тему История создания стихотворения М. Лермонтова “Нищий” 7 вопросов
- Тест на тему История создания стихотворения "Она сидела на полу" 7 вопросов
- Тест на тему История создания Пушкиным стихотворения "К морю" 6 вопросов
- Тест на тему История создания повести «Станционный смотритель» А. Пушкина 10 вопросов
- Тест на тему История создания «Оды на день восшествия» М. Ломоносова 7 вопросов
- Тест на тему Реферат по физкультуре на тему: «Здоровое питание» 5 вопросов
- Тест на тему История развития лыжного спорта в разных странах - классификация и интересные факты 6 вопросов
- Тест на тему Важность самоконтроля при занятиях спортом 5 вопросов
- Тест на тему Как выполняются прыжки через козла? 5 вопросов
- Тест на тему Что такое здоровый образ жизни? 5 вопросов
- Тест на тему Как правильно выполнять кувырки? 5 вопросов
- Тест на тему Развитие гибкости тела: упражнения и польза для тела 5 вопросов
- Тест на тему Виды и польза прыжков через скакалку 5 вопросов
- Тест на тему Какие есть зимние виды спорта? 5 вопросов
- Тест на тему Реферат на тему: “Гимнастика как вид спорта” 8 вопросов
- Тест на тему Реферат по физкультуре на тему “Футбол” 7 вопросов
- Тест на тему Реферат по физкультуре на тему: “Баскетбол - виды и лиги” 7 вопросов
- Тест на тему Реферат на тему «Лыжный спорт» 10 вопросов
- Тест на тему Реферат по физической культуре «Формы и виды закаливания» 10 вопросов
- Тест на тему Проект на тему: “Экономика родного края: Самарская область” 5 вопросов
- Тест на тему Как люди узнают о том, что было в прошлом? 5 вопросов
- Тест на тему Какие животные впадают в спячку зимой: объяснения зоологов 7 вопросов
- Тест на тему Сообщение по окружающему миру для 4 класса об острове Врангеля 5 вопросов
- Тест на тему Сообщение о морских обитателях - описание, виды и названия 7 вопросов
- Тест на тему Красный и белый террор в годы Гражданской войны 5 вопросов
- Тест на тему История появления имущественного неравенства и знати 5 вопросов
- Тест на тему Народы, населявшие Россию во второй половине 16 века 5 вопросов
- Тест на тему Первые государства: история образования и функции 5 вопросов
- Тест на тему Роль огня в жизни первобытных и современных людей 5 вопросов
- Тест на тему 5 самых известных разведчиков в истории 5 вопросов
- Тест на тему Присоединение к Московскому государству Смоленска 5 вопросов
- Тест на тему Причины и предпосылки объединения русских земель вокруг Москвы 5 вопросов
- Тест на тему Формирование русского централизованного государства 5 вопросов
- Тест на тему Краткая история Руси в 15 веке: главные события, культура 5 вопросов
- Тест на тему Причины и итоги установления автокефалии Русской Церкви 5 вопросов
- Тест на тему Особенности общественного строя и церковной организации на Руси 5 вопросов
- Тест на тему Когда появились первые известия о русских и Руси? 5 вопросов
- Тест на тему Призвание на княжение в Новгород варягов 5 вопросов
- Тест на тему История присоединения Псковского княжества к Московскому 5 вопросов
- Тест на тему История битв при Чашниках в 1564 и 1657 годах 5 вопросов
- Тест на тему Правление Василия 1 Дмитриевича 5 вопросов
- Тест на тему Земская реформа Ивана Грозного 5 вопросов
- Тест на тему Все князья Московского княжества 5 вопросов
- Тест на тему Причины, ход восстания Тадеуша Костюшко и его итоги 5 вопросов
- Тест на тему Последствия Смутного времени в России 5 вопросов
- Тест на тему Главные реформы короля Священной Римской империи Иосифа 2 5 вопросов
- Тест на тему Состав и функции государева двора 5 вопросов
- Тест на тему Суть “дела Дрейфуса” и реакция общества 5 вопросов
- Тест на тему Деятельность партии монтаньяров во Франции 5 вопросов
- Тест на тему Традиции и обычаи украинского народа 5 вопросов
- Тест на тему Причины закрытия Японии в 17 веке и последствия 5 вопросов
- Тест на тему Подготовка и содержание генерального плана “Ост” 5 вопросов
- Тест на тему Тайны убийства Петра Столыпина 5 вопросов
- Тест на тему Отмена подушной подати на Руси 5 вопросов
- Тест на тему Период регентства Елены Глинской: события и реформы 5 вопросов
- Тест на тему Экономика России в годы Первой мировой войны 5 вопросов
- Тест на тему Битва при деревне Лесной 28 сентября 1708 года 5 вопросов
- Тест на тему 10 любопытных фактов про Рождество 5 вопросов
- Тест на тему 10 любопытных фактов про Новый год 5 вопросов
- Тест на тему История потешных полков Петра Первого 5 вопросов
- Тест на тему Образование и распад тушинского лагеря при Лжедмитрии II 5 вопросов
- Тест на тему Чем ведал и какие функции выполнял Разрядный приказ? 5 вопросов
- Тест на тему Задачи и направления внешней политики России в 16 веке 5 вопросов
- Тест на тему Установление и отмена бессрочного сыска беглых крестьян на Руси 5 вопросов
- Тест на тему История создания и деятельности Вольного экономического общества 5 вопросов
- Тест на тему Период правления Вещего Олега: внешняя и внутренняя политика 5 вопросов
- Тест на тему Правление и политика князя Игоря 5 вопросов
- Тест на тему Суть и последствия Нерчинского договора России с Китаем 1689 года 5 вопросов
- Тест на тему Причины, ход и итоги войны за польское наследство 1733-1735 гг. 5 вопросов
- Тест на тему Восстановление экономики СССР после Великой Отечественной Войны 5 вопросов
- Тест на тему Как и зачем были созданы полки иноземного строя 5 вопросов
- Тест на тему Создание стрелецких войск при Иване Грозном 5 вопросов
- Тест на тему Причины, ход событий и итоги выступления старообрядцев при Петре I 7 вопросов
- Тест на тему Как и почему началась Ливонская война: основные причины 5 вопросов
- Тест на тему Особенности раздельного написания местоимений с предлогами 5 вопросов
- Тест на тему Правописание падежных окончаний прилагательных 5 вопросов
- Тест на тему Правописание слов с непроверяемой безударной гласной в корне 5 вопросов
- Тест на тему Нужно ли ставить запятую к фразе - "с уважением"? 5 вопросов
- Тест на тему «Во-вторых» или «во вторых» – как правильно пишется? 5 вопросов
- Тест на тему "Нету" или "нет" - как правильно писать и говорить? 5 вопросов
- Тест на тему «Не я» или «нея» – как правильно пишется? 5 вопросов
- Тест на тему «Полным-полно» или «полным полно» - как правильно пишется? 5 вопросов
- Тест на тему Как пишется «кто-нибудь» или «кто нибудь»? 5 вопросов
- Тест на тему Мягкий знак после шипящих в глаголах - правила, примеры 5 вопросов
- Тест на тему «Потвёрже» или «по твёрже» – как правильно пишется? 5 вопросов
- Тест на тему «Какой-то» или «какой то» – как пишется правильно? 5 вопросов
- Тест на тему «Мало-помалу» или «мало помалу» – как правильно пишется? 5 вопросов
- Тест на тему «По-осеннему» или «по осеннему» – как правильно пишется? 5 вопросов
- Тест на тему "Находу" или "на ходу" - слитно или раздельно писать? 5 вопросов
- Тест на тему "ЮлИчка" или "ЮлЕчка" - как правильно писать? 5 вопросов
- Тест на тему «Не пойму» или «непойму» – как правильно пишется? 5 вопросов
- Тест на тему «Доброе утро» − как правильно пишется? 5 вопросов
- Тест на тему «Почему-то» или «почему то» – как правильно пишется? 5 вопросов
- Тест на тему «На вынос» или «навынос» – как правильно пишется? 5 вопросов
- Тест на тему «Невежливо» или «не вежливо» – как правильно пишется? 5 вопросов
- Тест на тему «Негодуя» или «не годуя» - как правильно пишется? 5 вопросов
- Тест на тему «КуриНый» или «куриННый» − как правильно пишется? 5 вопросов
- Тест на тему «ТеННис» или «теНис» – как правильно пишется? 5 вопросов
- Тест на тему «ТумаННый» или «тумаНый» – как правильно пишется? 5 вопросов
- Тест на тему «ЗамечеННый» или «замечеНый» – как правильно пишется? 5 вопросов
- Тест на тему «Семнадцать» или «семЬнадцать» – как правильно пишется? 5 вопросов
- Тест на тему «ВыздОравливающий» или «выздАравливающий» – как правильно пишется? 5 вопросов
- Тест на тему «Свеж» или «свежЬ» – как правильно пишется? 5 вопросов
- Тест на тему «СлаЩе» или «слаДЧе» – как правильно пишется? 5 вопросов
- Тест на тему «ПрЕтерпевать» или «прИтерпевать» - как правильно пишется? 5 вопросов
- Тест на тему «Удастся» или «удастЬся» – как правильно пишется? 5 вопросов
- Тест на тему «СписаНо» или «СписаННо» – как правильно пишется? 5 вопросов
- Тест на тему «Происшествие» или «проишествие» – как правильно пишется? 5 вопросов
- Тест на тему «НачИнающий» или «начЕнающий» – как правильно пишется? 5 вопросов
- Тест на тему «Невозможно» или «не возможно» – как пишется слитно или раздельно? 5 вопросов
- Тест на тему «Налету» или «на лету» – как правильно пишется? 5 вопросов
- Тест на тему «Надолго» или «на долго» – как правильно пишется? 5 вопросов
- Тест на тему «ПьющАя» или «пьющЕя» – как правильно пишется? 5 вопросов
- Тест на тему «Неужели» или «не ужели» − как правильно пишется? 5 вопросов
- Тест на тему «НИкого» или «нЕкого» – как правильно пишется? 5 вопросов
- Тест на тему «БаССейн» или «баСейн» − как правильно пишется? 5 вопросов
- Тест на тему "Не согласованно" или "несогласованно" - слитно или раздельно? 5 вопросов
- Тест на тему «ОбстОятельствам» или «обстАятельствам» – как правильно пишется? 5 вопросов
- Тест на тему «ОбижеННый» или «обижеНый» – как правильно пишется? 5 вопросов
- Тест на тему «Аллах» или «Алах» – как правильно пишется? 5 вопросов
- Тест на тему «БелОрусский» или «белАрусский» – как правильно пишется? 5 вопросов
- Тест на тему «ЧИсло» или «чЕсло» – как правильно пишется? 5 вопросов
- Тест на тему «УвЕряющий» или «увИряющий» – как правильно пишется? 5 вопросов
- Тест на тему «НенасТный» или «ненасный» – как правильно пишется? 5 вопросов
- Тест на тему Анализ стихотворения “Каким бы малым ни был...” К. Кулиева 5 вопросов
- Тест на тему Анализ стихотворения «Цицерон» Ф. Тютчева 5 вопросов
- Тест на тему Анализ стихотворения “Поэт” М. Лермонтова 5 вопросов
- Тест на тему Анализ стихотворения “Пора, мой друг, пора” А. Пушкина 5 вопросов
- Тест на тему Анализ стихотворения «Шестое чувство» Н. Гумилева 5 вопросов
- Тест на тему Анализ стихотворения “Юбилейное” В. Маяковского 5 вопросов
- Тест на тему Анализ стихотворения “Мой гений” К. Батюшкова 5 вопросов
- Тест на тему Анализ стихотворения «Нет, не тебя так пылко» М. Лермонтова 5 вопросов
- Тест на тему Анализ стихотворения «Догорел апрельский светлый вечер…» И. Бунина 5 вопросов
- Тест на тему Анализ стихотворения «Фонтан» Ф. Тютчева 5 вопросов
- Тест на тему Анализ стихотворения «Посмотри - какая мгла» Я. Полонского 5 вопросов
- Тест на тему Анализ стихотворения «Школьник» Н. Некрасова 5 вопросов
- Тест на тему Анализ стихотворения «Несжатая полоса» Н. Некрасова 5 вопросов
- Тест на тему «Весенний дождь» - анализ стихотворения А.А. Фета 7 вопросов
- Тест на тему «Поет зима - аукает» - анализ стихотворения С.А. Есенина 7 вопросов
- Тест на тему Краткое содержание повести «А тем временем где-то» А. Алексина 5 вопросов
- Тест на тему Краткое содержание комедии «Мнимый больной» Жана-Батиста Мольера 5 вопросов
- Тест на тему Краткое содержание комедии “Доходное место” А. Островского 5 вопросов
- Тест на тему Краткое содержание новеллы “Падение дома Ашеров” Эдгара По 5 вопросов
- Тест на тему Краткое содержание рассказа “Крепкий мужик” В. Шукшина 5 вопросов
- Тест на тему Краткое содержание пьесы «Золотая карета» Л. Леонова 5 вопросов
- Тест на тему Краткое содержание рассказа «Когда в доме одиноко» К. Саймака 5 вопросов
- Тест на тему Краткое содержание рассказа “Простите нас” Ю. Бондарева 5 вопросов
- Тест на тему Краткое содержание романа “Кысь” Т. Толстой 5 вопросов
- Тест на тему Краткое содержание повести “Это мы, Господи!” К. Воробьева 5 вопросов
- Тест на тему Краткое содержание романа «Как закалялась сталь» Н. Островского 5 вопросов
- Тест на тему Краткое содержание романа-эпопеи «Хождение по мукам» А. Толстого 5 вопросов
- Тест на тему Краткое содержание сказки “Журавль и цапля” 5 вопросов
- Тест на тему Краткий пересказ “О чем говорят цветы” Жорж Санд 5 вопросов
- Тест на тему Краткое содержание рассказа “Тринадцать лет” С. Баруздина 5 вопросов
- Тест на тему Краткое содержание рассказа «Парадокс» В. Короленко 5 вопросов
- Тест на тему Краткое содержание романа «Живые и мертвые» К. Симонова 5 вопросов
- Тест на тему Краткое содержание повести «Обмен» Юрия Трифонова 5 вопросов
- Тест на тему Краткое содержание рассказа “Алешкино сердце” М. Шолохова 5 вопросов
- Тест на тему Краткое содержание рассказа “Как я стал писателем” И. Шмелева 5 вопросов
- Тест на тему Краткое содержание рассказа “Гамбринус” А. Куприна 5 вопросов
- Тест на тему Краткое содержание сказки “Вафельное сердце” Марии Парр 5 вопросов
- Тест на тему Краткое содержание рассказа “Специалист” А. Аверченко 5 вопросов
- Тест на тему Краткое содержание пьесы «Трамвай “Желание”» Т. Уильямса 5 вопросов
- Тест на тему Краткое содержание романа “Война миров” Г. Уэллса 5 вопросов
- Тест на тему Краткое содержание рассказа “Баргамот и Гараська” Л. Андреева 5 вопросов
- Тест на тему Краткое содержание повести “Скотный двор” Д. Оруэлла 5 вопросов
- Тест на тему «Акула» Л. Толстого - краткое содержание 5 вопросов
- Тест на тему Русская народная сказка «Хвосты» - краткое содержание 5 вопросов
- Тест на тему Краткое содержание оперы «Снегурочка» Римского-Корсакова 5 вопросов
- Тест на тему «Обезьяний язык» М. Зощенко – краткое содержание 10 вопросов
- Тест на тему «Сердце не камень» - краткое содержание пьесы А.Н. Островского 5 вопросов
- Тест на тему Балет «Щелкунчик» — краткое содержание 7 вопросов
- Тест на тему Биография Владимира Вольфовича Жириновского 5 вопросов
- Тест на тему Биография поэта и писателя Льва Рубинштейна 5 вопросов
- Тест на тему Биография президента Белоруссии Александра Лукашенко 5 вопросов
- Тест на тему 10 интересных фактов про Афанасия Фета 5 вопросов
- Тест на тему 10 интересных фактов про Ивана Тургенева 5 вопросов
- Тест на тему Биография писателя и поэта Вячеслава Урюпина 5 вопросов
- Тест на тему Биография поэта Николая Михайловича Рубцова 5 вопросов
- Тест на тему Биография поэта Андрея Дмитриевича Дементьева 5 вопросов
- Тест на тему Биография президента РФ Владимира Путина 5 вопросов
- Тест на тему Биография и личная жизнь Даниила Хармса 5 вопросов
- Тест на тему Краткая биография Валентины Осеевой 5 вопросов
- Тест на тему Григорий Остер: биография писателя и избранные произведения 7 вопросов
- Тест на тему Елена Благинина: творческая биография и личная жизнь 10 вопросов
- Тест на тему Биография детской писательницы Ирины Пивоваровой 5 вопросов
- Тест на тему История создания рассказа «Матренин двор» А. Солженицына 5 вопросов
- Тест на тему История создания песни «Смуглянка» 5 вопросов
- Тест на тему История создания поэмы “Кому на Руси жить хорошо” Н. Некрасова 5 вопросов
- Тест на тему История создания романа “Как закалялась сталь” Н. Островского 5 вопросов
- Тест на тему История создания оперы М. Глинки «Иван Сусанин» 5 вопросов
- Тест на тему История создания знаменитой песни “Катюша” 5 вопросов
- Тест на тему История создания поэмы “За далью - даль” А. Твардовского 5 вопросов
- Тест на тему История создания стихотворения “Смерть поэта” М. Лермонтова 5 вопросов
- Тест на тему История создания рассказа “Кавказский пленник” Л. Н. Толстого 5 вопросов
- Тест на тему История создания песни Р. Гамзатова “Журавли” 5 вопросов
- Тест на тему История создания стихотворения “Зимнее утро” А. С. Пушкина 5 вопросов
- Тест на тему История создания рассказа "Судьба человека" М. Шолохова 5 вопросов
- Тест на тему История создания стихотворения "На холмах Грузии лежит ночная мгла..." А. Пушкина 5 вопросов
- Тест на тему История создания романа “Идиот” Ф. М. Достоевского 5 вопросов
- Тест на тему История создания рассказа «Васюткино озеро» В. Астафьева 5 вопросов
- Тест на тему История создания повести “Детство” Л. Толстого 5 вопросов
- Тест на тему История создания романа «Дон Кихот» М. Сервантеса 5 вопросов
- Тест на тему История создания романа «Бесы» Ф. Достоевского 5 вопросов
- Тест на тему История создания романа «Молодая гвардия» А. Фадеева 5 вопросов
- Тест на тему История создания пьесы «Моцарт и Сальери» А. С. Пушкина 5 вопросов
- Тест на тему История создания баллады «Лесной царь» Ф. Шуберта 5 вопросов
- Тест на тему "Миссия русской эмиграции" И. Бунина 5 вопросов
- Тест на тему История создания пьесы «Бесприданниц» А. Островского 5 вопросов
- Тест на тему История создания повести “Алые паруса” А. Грина 1 вопрос
- Тест на тему История создания романа “Бедные люди” Ф. Достоевского 5 вопросов
- Тест на тему Герои романа “Властелин колец” Д. Толкина 5 вопросов
- Тест на тему Анализ сказа “Серебряное копытце” П. Бажова 5 вопросов
- Тест на тему Характеристика Дуняши в романе “Тихий Дон” М. Шолохова 5 вопросов
- Тест на тему Описание образа Фамусова - персонажа комедии “Горе от ума” 5 вопросов
- Тест на тему Характеристика образа Сатина - персонажа пьесы “На дне” М. Горького 5 вопросов
- Тест на тему Анализ повести “Сашка” В. Кондратьева 5 вопросов
- Тест на тему Характеристика образа Фауста из трагедии Гёте 9 вопросов
- Тест на тему Анализ романа “Портрет Дориана Грея” О. Уайльда 5 вопросов
- Тест на тему Характеристика колобка - героя русской народной сказки 5 вопросов
- Тест на тему Образ главной героини “Алисы в стране чудес” Л. Кэррола 5 вопросов
- Тест на тему Трактовки образа Иисуса Христа в поэме “Двенадцать” А. Блока 5 вопросов
- Тест на тему Образ Настеньки из повести “Белые ночи” Ф. Достоевского 5 вопросов
- Тест на тему Конфликт в рассказе “После бала” Л. Толстого 5 вопросов
- Тест на тему Образ главной героини повести “Бедная Лиза” Н. Карамзина 5 вопросов
- Тест на тему Описание образа Васютки из рассказа “Васюткино озеро” В. Астафьева 5 вопросов
- Тест на тему Образы чиновников в комедии “Ревизор” Н. Гоголя 5 вопросов
- Тест на тему Роль образа вишневого сада в пьесе А. Чехова 5 вопросов
- Тест на тему Характеристика профессора Преображенского в повести “Собачье сердце” М. Булгакова 5 вопросов
- Тест на тему Описание образа городничего в комедии “Ревизор” Н. Гоголя 5 вопросов
- Тест на тему Описание образа главного героя “Доктора Живаго” Б. Пастернака 5 вопросов
- Тест на тему Образ Цыганка в повести “Детство” М. Горького 5 вопросов
- Тест на тему Характеристика Вани Солнцева в повести “Сын полка” В. Катаева 5 вопросов
- Тест на тему Образ автора в поэме "Василий Теркин" А. Твардовского 5 вопросов
- Тест на тему Образ портрета в повести "Портрет" Н. В. Гоголя 5 вопросов
- Тест на тему Описание образа девушки-ундины из “Героя нашего времени” М. Лермонтова 5 вопросов
- Тест на тему Как выполнить разбор наречия по составу 5 вопросов
- Тест на тему Правила правописания суффиксов наречий 5 вопросов
- Тест на тему Морфологический признак наречий: неизменяемость 5 вопросов
- Тест на тему Чем отличаются и как найти тему и рему в тексте? 5 вопросов
- Тест на тему Способы и примеры образования наречий 5 вопросов
- Тест на тему Особенности и применение составных предлогов 5 вопросов
- Тест на тему Какую синтаксическую роль в предложении выполняет наречие 5 вопросов
- Тест на тему Какие признаки прилагательного есть у причастия 5 вопросов
- Тест на тему Морфологический разбор союзов: инструкция, примеры 5 вопросов
- Тест на тему Морфологические признаки действительных и страдательных причастий 5 вопросов
- Тест на тему Особенности и примеры звукоподражательных слов 5 вопросов
- Тест на тему Какие бывают и как определить смысловую группу наречий 5 вопросов
- Тест на тему Неправильное построение предложений с косвенной речью: примеры ошибок 5 вопросов
- Тест на тему Расстановка знаков препинания в сложноподчиненных предложениях 5 вопросов
- Тест на тему Виды синтаксических связей в словосочетаниях и предложениях 5 вопросов
- Тест на тему Оформление и примеры несобственно-прямой речи в тексте 5 вопросов
- Тест на тему Структура текста с параллельной связью предложений 5 вопросов
- Тест на тему Литературный язык: понятие, признаки, формы 5 вопросов
- Тест на тему Функции и роль языка в жизни человека и общества 5 вопросов
- Тест на тему Сообщение на тему: «Традиции русской речевой манеры общения» 5 вопросов
- Тест на тему Определение и виды простых осложненных предложений 5 вопросов
- Тест на тему Какие бывают виды текстов? 5 вопросов
- Тест на тему Образование и правописание страдательных причастий настоящего времени 5 вопросов
- Тест на тему Как определить начальную форму прилагательного? 5 вопросов
- Тест на тему Местоимение-прилагательное в русском языке 5 вопросов
- Тест на тему Сборник правил по русскому языку для 6 класса 7 вопросов
- Тест на тему Сборник правил по русскому языку за 5 класс 7 вопросов
- Тест на тему Упражнения для тренировки школьников 7 класса по причастному обороту 9 вопросов
- Тест на тему Тест: Склонение фамилий в русском языке 7 вопросов
- Тест на тему Общеупотребительные и необщеупотребительные слова 5 вопросов
- Тест на тему Дефисное и слитное написание сложных прилагательных 5 вопросов
- Тест на тему Морфологический разбор числительного - правило и примеры 5 вопросов
- Тест на тему Уровень урбанизации Африки: города растут, вызовы множатся 5 вопросов
- Тест на тему Уровень и особенности урбанизации Канады 5 вопросов
- Тест на тему Как найти полярную звезду и зачем ее искать? 5 вопросов
- Тест на тему Что нужно знать про контурные карты 5 вопросов
- Тест на тему Кто, когда и как открыл Австралию? 5 вопросов
- Тест на тему Характеристика природных зон Поволжья 5 вопросов
- Тест на тему Для каких рек в России характерно летнее половодье? 5 вопросов
- Тест на тему Как правильно заполнять дневник наблюдения за погодой 5 вопросов
- Тест на тему Влажные экваториальные леса - особенности климата, характеристика флоры и фауны 7 вопросов
- Тест на тему Европейский север России - географическое положение, особенности развития предприятий и промышленности 7 вопросов
- Тест на тему Что такое масштаб карты и как его определять 7 вопросов
- Тест на тему Особенности и примеры островных государств 5 вопросов
- Тест на тему Природные зоны Южной Америки - характеристики и особенности 7 вопросов
- Тест на тему 10 интересных фактов про океан 7 вопросов
- Тест на тему Сектор Газа: где он находится и откуда такое название? 6 вопросов
- Тест на тему "Банты" - как правильно ставить ударение в слове? 5 вопросов
- Тест на тему «Конечно же» - выделяется ли слово запятыми? 5 вопросов
- Тест на тему «Подчеркивать» – как правильно ставить ударение в слове? 5 вопросов
- Тест на тему «Лифты» – как правильно ставить ударение в слове? 5 вопросов
- Тест на тему «Строку» – как правильно ставить ударение в слове? 5 вопросов
- Тест на тему «Апостроф» – как правильно ставить ударение в слове? 5 вопросов
- Тест на тему «Зубчатый» – как правильно ставить ударение в слове? 5 вопросов
- Тест на тему «Прозорлива» – как правильно ставить ударение в слове? 5 вопросов
- Тест на тему «Балашиха» – как правильно ставить ударение в слове? 5 вопросов
- Тест на тему «Реку» – как правильно ставить ударение в слове? 5 вопросов
- Тест на тему «Полно» – как правильно ставить ударение в слове? 5 вопросов
- Тест на тему «Говорено» – как правильно ставить ударение в слове? 5 вопросов
- Тест на тему «Досыта» – как правильно ставить ударение в слове? 5 вопросов
- Тест на тему «Упрочение» – как правильно ставить ударение в слове? 5 вопросов
- Тест на тему «Развила» – как правильно ставить ударение в слове? 5 вопросов
- Тест на тему «Подолгу» – как правильно ставить ударение в слове? 5 вопросов
- Тест на тему «Логин» – как правильно ставить ударение в слове? 5 вопросов
- Тест на тему «Окон» – как правильно ставить ударение в слове? 5 вопросов
- Тест на тему «Втридорога» – как правильно ставить ударение в слове? 5 вопросов
- Тест на тему «Утра» – как правильно ставить ударение в слове? 5 вопросов
- Тест на тему «Запломбированный» – как правильно ставить ударение в слове? 5 вопросов
- Тест на тему «Цыган» – как правильно ставить ударение в слове? 5 вопросов
- Тест на тему «Шарфы» – как правильно ставить ударение в слове? 5 вопросов
- Тест на тему «Бармен» – как правильно ставить ударение в слове? 5 вопросов
- Тест на тему «Положенный» – как правильно ставить ударение в слове? 5 вопросов